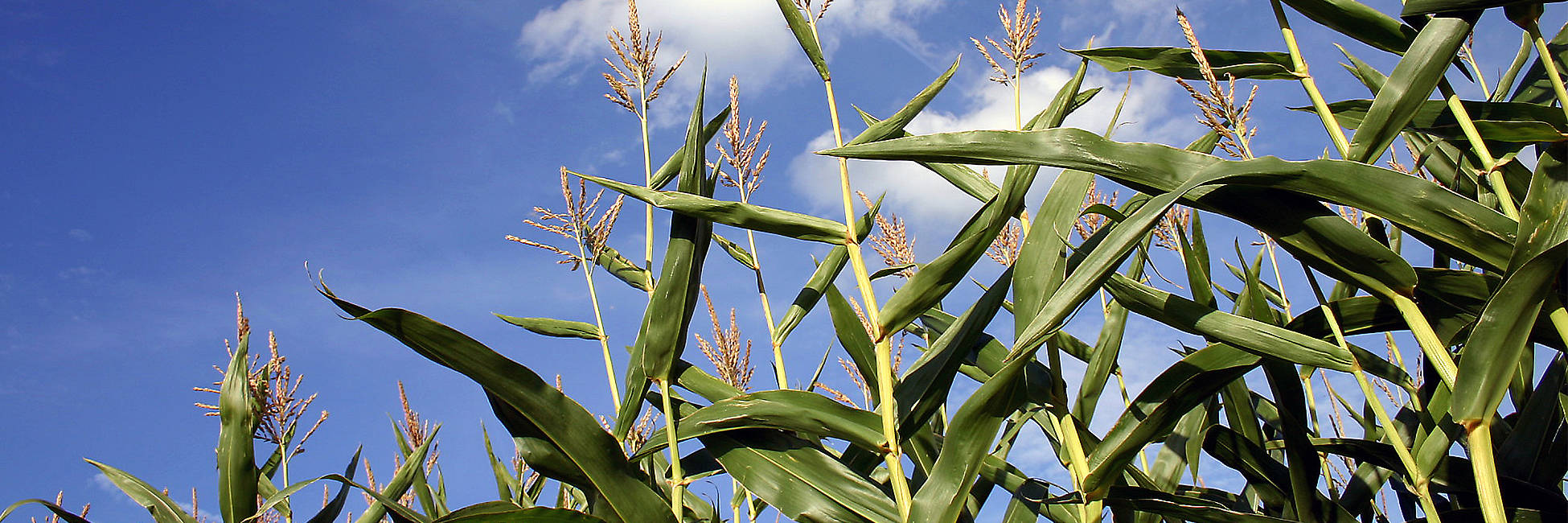
Our engineers combine their many years of experience of planning technical processes with innovative concepts to create a safe and reliable process, which is a very cost-effective and reliable solution for trouble-free plant operation.
In addition to the production of bioethanol for use as a biofuel, the production of biogas and the brewery are counted among the focus of the fermentation industry.
We also plan complete industrial processing plants for the deep processing of molasses – which is formed as a byproduct in sugar refineries – to create a range of fermentation products. Fermentation plants cover all the stages, from the acceptance and processing of the substrate, through the fermentation, to the downstream processes and packaging.
The EPC Group applies the state-of-the-art technologies to plan and construct fermentation plants that conform to the requirements of Food and Drug Administration (FDA) and Good Manufacturing Practice (GMP).
The viscosity controlling properties of xanthan make it a preferred gelling and film-forming agent in the foodstuffs industry. Xanthan is also used in some specialist fields, such as crude oil and ore extraction. Xanthan is an approved food additive in Europe, with the assigned number E415.
EPC's specialists supervise the experimental process and optimized the plant parameters. The process is simulated in pilot scale, and the data required for the scaling up procedure are determined. The methods developed in laboratory scale can be used with a large scale-up factor for operations in the technical production plant.
Our engineers are principally involved in processes, in which the chemical, mechanical and microbiological transformation of substances is accompanied by a material, heat and impulse exchange. These processes usually behave differently at small laboratory scale than they do at large production scale; the scale-up is our expertise!
Whereas the enzyme method uses enzymes as biocatalysts, the fermentation method uses the natural biochemical reactions of living cells, which create and transform substances. The main priority is for all the products to be characterized by perfect quality and pioneering innovation. The EPC Group is conscious of these quality standards, and constructs fermentation plants on the basis of the latest technologies that conform to the requirements of Food and Drug Administration (FDA) and Good Manufacturing Practice (GMP).
As some essential proteins cannot be produced by the organism itself, they have to be added, for example, to animal feed as a nutritional supplement. The resulting high protein fodder has muscle-building and performance enhancing effects in comparison to conventional animal feed.
Vegetable proteins are mainly obtained as by-products from the press residues of oil pressing and extraction processes. Depending on the type of raw material or the use of the product, the press cake is processed by either an "alcoholic" or an "aqueous" method.
Alcoholic extraction, usually with ethanol, achieves a higher yield and a purer protein, but more apparatus is required for the more intensive purification of the protein.
Setting the pH value is crucial to obtaining optimal separation of the protein by means of acid-base washing. We offer integrated concepts for controlling the recirculation of process water and water treatment, which minimize process costs and ensure environmentally friendly operation.
The selection of the most suitable process for obtaining protein is based on our experience in the fields of plant engineering and operational management, and an evaluation of the current market situation. We collaborate intensively with experienced, well-regarded equipment suppliers and our customers to work out an optimal, profitable and goal-oriented process variant.