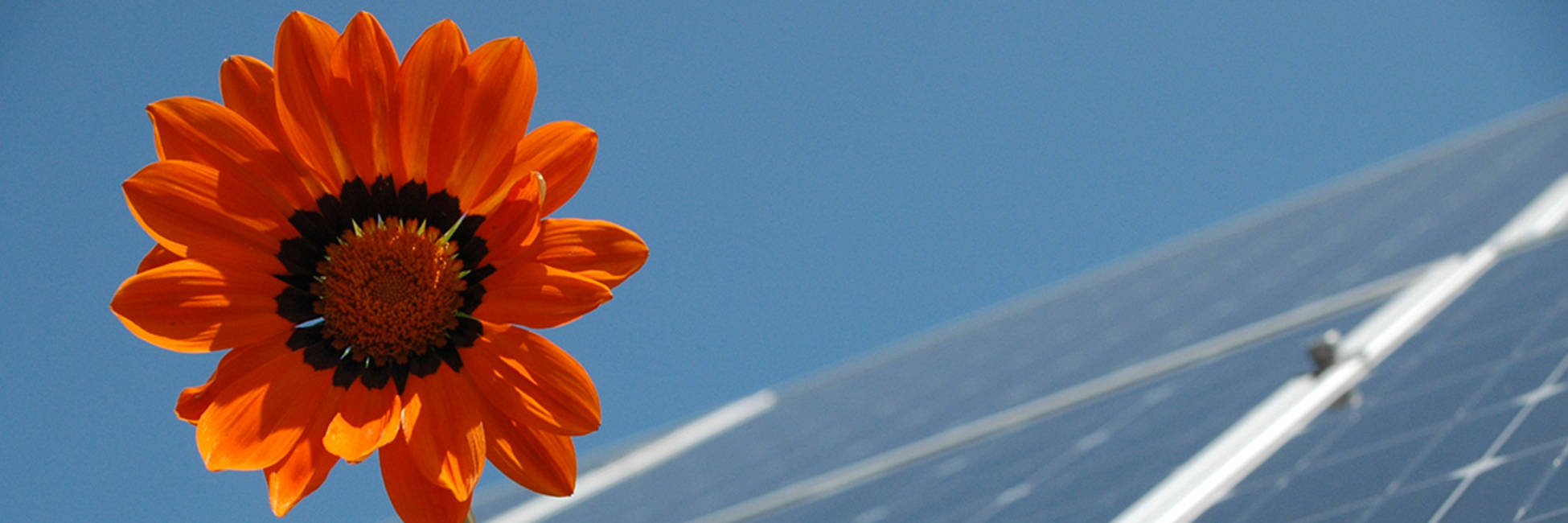
Our lives literally revolve around the sun. Its almost inexhaustible power inspires many ideas and developments. For our customers, it is a valuable source of energy that can be used technically in the form of electricity, heat or chemical energy. Sunbeams are electromagnetic waves. The amount of energy that reaches the surface of the earth each year is more than 5,000 times greater than humanity's total energy requirement. Solar energy reduced CO2 emissions by 3.6 million tons.
Environmental protection and reduced depletion of resources are just two of the benefits resulting from the use of solar energy. The solar industry has developed into an important sector of the economy, and it is also a major employer.
EPC can look back on many years of wide-ranging experience of designing plants for the solar industry, such as plants for manufacturing ultrapure silicon, and solar factories for producing ingots, wafers and modules. All our know-how is also at your service to help you plan the delivery, commissioning and maintenance of important subsidiary processes, such as slurry handling systems, waste gas cleaning, monosilane and hazardous substance stores, as well as supply and disposal systems. Evaluation of the economic efficiency along the entire value added chain, from the project idea through to the finished concept, is the essential factor that ensures that your plant will run profitably and remain competitive in the market over the long term.
The EPC Group offers its customers all the know-how along the entire added value chain required to construct plants for the solar industry. We design plants for manufacturing ingots, wafers, cells and modules, together with all the ancillary plants for exhaust air and waste water treatment, redundant power supplies, hazardous substance stores and handling systems for monosilane and other essential substances. As an experienced general planner, we can assist at every stage of the construction of a new solar factory, or the extension and renovation of an existing factory.