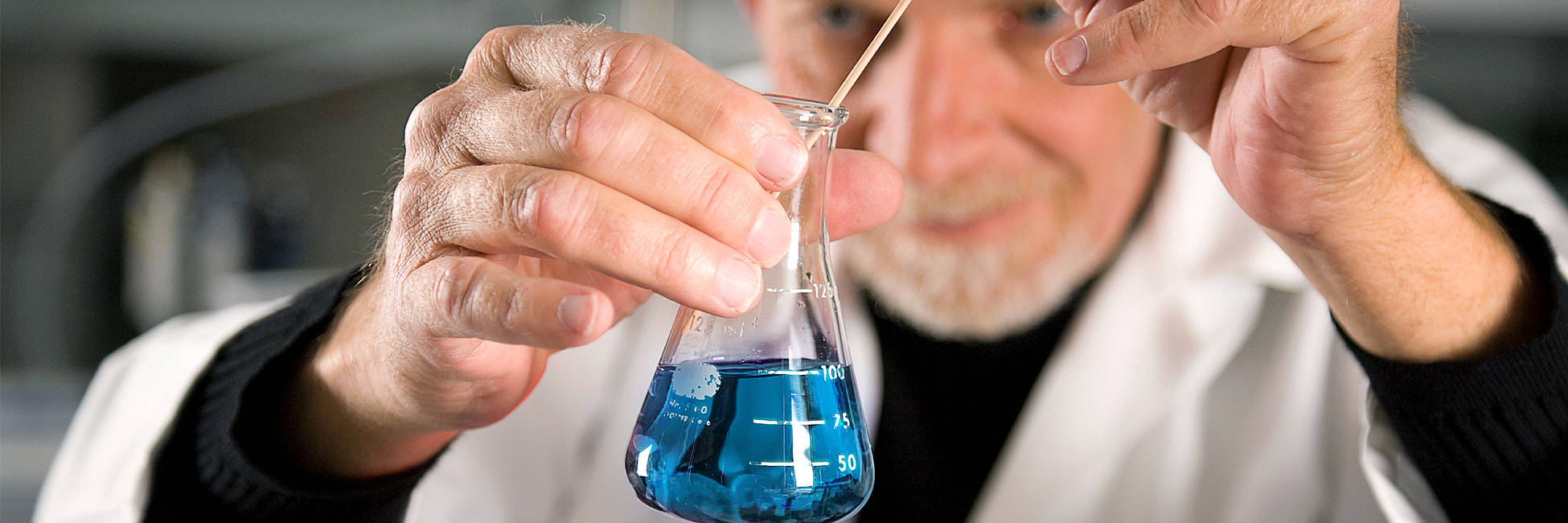
In the case of multi-purpose plants, either reference syntheses and their minimum requirements are defined, or the limit values for using the plant are derived from the configuration.
The plant uses hazardous substances subject to the Hazardous Substances Order, which have the following properties: extremely flammable, highly flammable, very toxic, toxic, harmful, irritant, corrosive, sensitising, an occupational exposure limit value. Notices are available that describe the CMR properties of the substances used: EU category 2 or 3 (GHS category 1B or 2). A hazardous explosive atmosphere can develop in the plant area as per (TRBS (German Technical Rules for Operational Safety) 2152 Part 1. Liquids subject to the German Water Ecology Act are used in the plant (plant for producing, treating and using substances).
(Hydration reactor for synthesizing hexenol at 100 bar(g) in a salt bath reactor at +400 °C)
On the other hand, diverse reactions are controlled in a low temperature range
(Highly reactive substances, selective isomerisation, etc.)