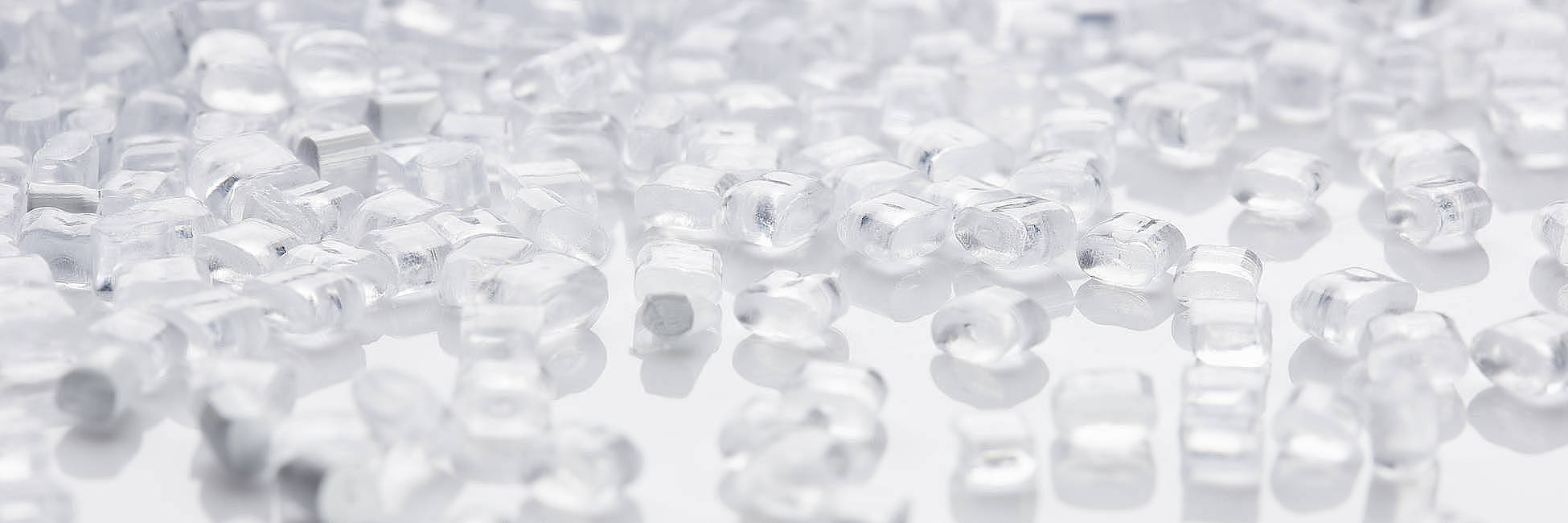
Таким образом, за последние годы было спроектировано и построено большое количество исследовательских и пилотных установок. Самый последний пример – это демонстрационная установка производства углеродного волокна от ЕРС. Она предлагает абсолютно новый опыт знакомства с возможностями большой установки. Поскольку эти новые миниатюрные версии промышленных производственных установок идеально подходят для опытов по формованию, разработки рецептур и оптимизации продукции, и конечно, для обучения персонала.
Очень легко использовать все стандартные органические растворители в, так называемой, «белой линии» (установка производства формовочного раствора и прекурсора формования), и для организации всех стадий последующей обработки волокна таким же образом, как они реализуются на крупномасштабных установках, и таким путем достичь сравнимого качества продукции.
Специфические преимущества окисления углеродного волокна – карбонизация на нашей установке, часто называется «черной линией», заключаются не только в точном управлении воздухом и температурой, но также в большом постоянстве температуры по всей длине волокна. Это достигается при помощи нагнеталей горячего газа и нагрева поверхности низкотемпературной печью. Равномерная температура достигается при помощи высокотемпературной печи путем принудительной циркуляции нагрева вокруг муфелов.
Технология:
EPC variPLANT® предоставляет Вам следующие конкурентные преимущества:
EPC PETvantage® является самой эффективной по затратам альтернативой для инвестиции в новую установку. В зависимости от конфигурации установки, возврат инвестиций, как правило, достигается менее чем за 2 года. В большинстве случаев, нет необходимости в замене основного реактора. Безопасность функционирования, качество продукции и производственные мощности увеличиваются в разы, в зависимости от базового проекта по установке и доступного места на площадке.
EPC PETvantage® генерирует высокую доходность, главным образом благодаря гарантии качества и соответственно большей конкурентоспособности:
EPC insidePET® представляет операционное ПО, разработанное для полностью автоматического функционирования и контроля качества на установка, которые использую инновационные технологические процессы по полиэфиру от ЕРС. EPC insidePET® уравнивает даже колебания качества сырья. Постоянство качества конечной продукции, производимой существующей установкой, в значительной степени улучшается благодаря всеобъемлющему и продуманному управлению процессом.
Мы предлагаем EPC insidePET®, либо как стандартное единичное решение или совместно с оптимизацией процесса и получением более высокой производительности полученной благодаря нашей проверенной и опробованной технологии EPC PETvantage®.
Коммерческие и качественные преимущества EPC insidePET®:
Компания ЕРС обладает обширным опытом в индустрии производства полимеров и волокон, и предлагает комплексные инжиниринговые решения для поставки производственных установок для полимеров/волокон мирового уровня. Для производства высококачественных ПЭТФГ, ПХТ, ПХТГ и ПХТК компания ЕРС Group предлагает свою современную технологию Гидрирования CHDM для производства первоклассных марок CHDM.
Эффективный и гибкий непрерывный технологический процесс гидрирования гарантирует стабильное производство CHDM высшего качества. Кроме того, наличие Вашей собственной передовой производственной линии CHDM обеспечит непрерывную поставку высококачественного CHDM в качестве сырья для производства ценных полиэфирных смол для быстро растущего применения в электронике, упаковке пищевых и медицинских продуктов, строительных элементах и потребительских товарах.
В производственном процессе желаемые аддитивы добавляются к сырьевым полимерным материалам в миксере, затем смесь перерабатывается в экструдере. Расплав в последующем пропускается через ванну охлаждения и после затвердевания подается на порезку в грануляторе. С процессом производства мастербэтчей фирма ЕРС предлагает своим клиентам возможность быстрой переориентировки на другую продукцию в пределах установки при минимальных усилиях для чистки. Энергоэффективные экструдерные системы являются прочными и экономически эффективными. Отходящее тепло из экструдера подается в установку и снова используется.
18%, достигается значительно более продолжительное время удержания. Поэтому это значительно минимизирует колебания качества концентрата экстракта. Разработанный фирмой ЕРС процесс экстракции может без больших инвестиционных затрат или долгих сроков модернизации функционировать на уже существующих установках. Посредством специального механизма азот распределяется до 16 зон экстракции в колонне. Гранулят поступает сверху вниз через слой засыпки в механизме. Азот и водный экстракт подаются в противоход вверх. Механизм состоит из наложенных друг на друга отсеков Азот распределяется равномерно по всем этим отсекам в поперечном сечении колонны. Такие отсеки оснащаются местами сужения, объединенной газовой камерой, состоящей из распределяющих ребер и периферического кольца. Имеется возможность выравнивания давления азота в отсеках за счет разрывов в распределительных ребрах и подачи и одновременного отсоса газов в сечении колонны на случай различия давления между местами сужения и отсеками из-за различного количества газов.
Преимущества запатентованного решения от ЕРС:
Предыдущие поколения реакторов, как правило, должны заменяться через несколько лет работы из-за эрозии материала. Фирма ЕРС разработала реактор для материала на основе специального алюминиевого сплава, который инертен к условия реакции (нет износа материала), и в последующем не имеет никакого влияния на среду реакции (никакого неконтролируемого поведения в реакции). Этот материал используется при производстве реактора и для стадий на входе и выходе в связи с реакцией полимеризации.
Компоненты установки, произведенные из такого материала не должны заменяться в течение всего запланированного срока эксплуатации установки. Посредством избежания отложений достигается увеличение производственных циклов. Необходимость более редкой чистки увеличивает производительность и уменьшает применение чистящих средств. Материал имеет прочностные характеристики, аналогичные как у стали, и может быть использован в обычных механических процессах и процессах формования (вальцевания, гибка, шлифовка, полировка, сварка).