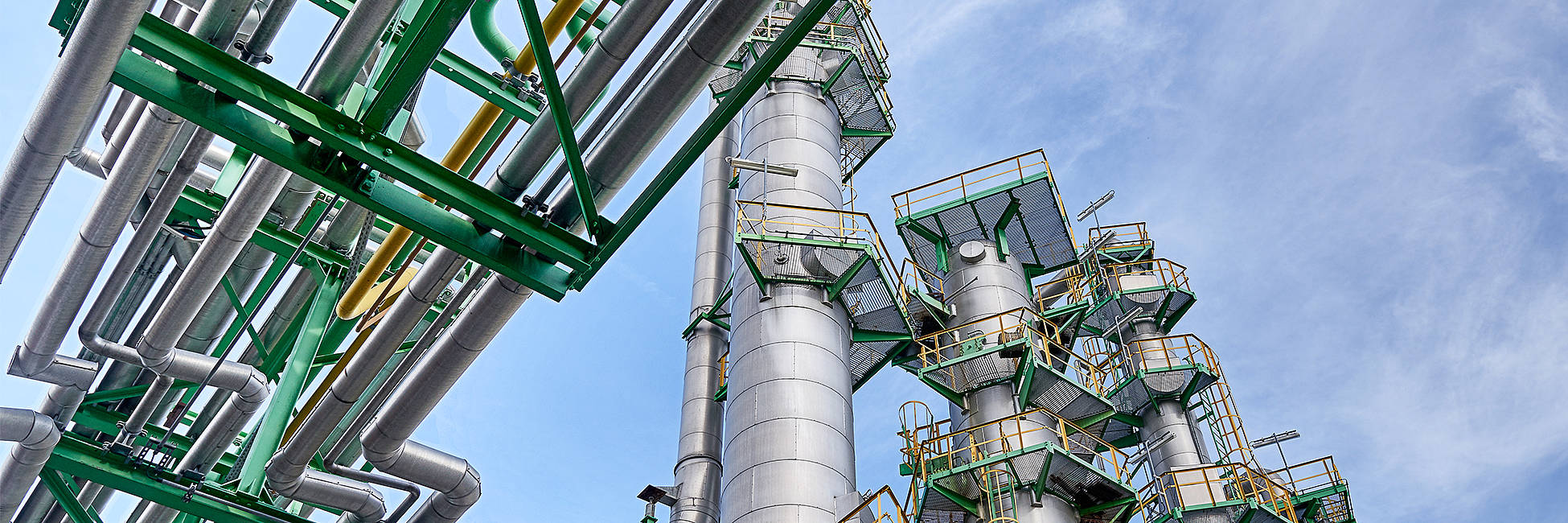
Aromatic benzene is used in the chemical industry as a raw material for making many organic and aromatic compounds. It is the starting material for the production of paints, plastics, synthetic resins, solvents, plant protection products and detergents. Benzene increases the octane number of petrol, and improves its anti-knock properties. Benzene is hydrogenated to produce acetone and phenol, as well as other compounds. Phenol is an equally important industrial chemical. It is used as an intermediate product in the production of plastics.
EPC offers you a selection of modern processes for the production of benzene and phenol, as well as wide choice state-of-the art technologies. EPC focuses on both the economic and the ecological aspects.
Despite the continual further developments of the technologies, the experts at EPC apply all their thinking to ensuring that caprolactam plants continue to remain commercially viable and environmentally compatible, with or without the production of ammonium sulfate.
Here again, EPC has the specific know-how that enables customers all over the world to produce granulates with an extremely low proportion of residues in the extraction. The granulates are used, for example, in the food industry.
The chemistry experts at EPC recommend using the commercially proven "big crystal-crystallization" process to achieve a really high-quality product. It is admittedly a complex process, but it is stable and flexible, and produces top quality ammonium sulfate with the aid of hydraulic classifying device equipment. The use of this modern technology offers many advantages. The heat and steam produced during the "big crystal-crystallization" process are recycled to reduce energy consumption to a very low level.
The substantial reduction of energy costs coupled with the high environmental compatibility due to the small quantities of wastes, and a top-class product enable you to look forward to a lucrative return on your investment.