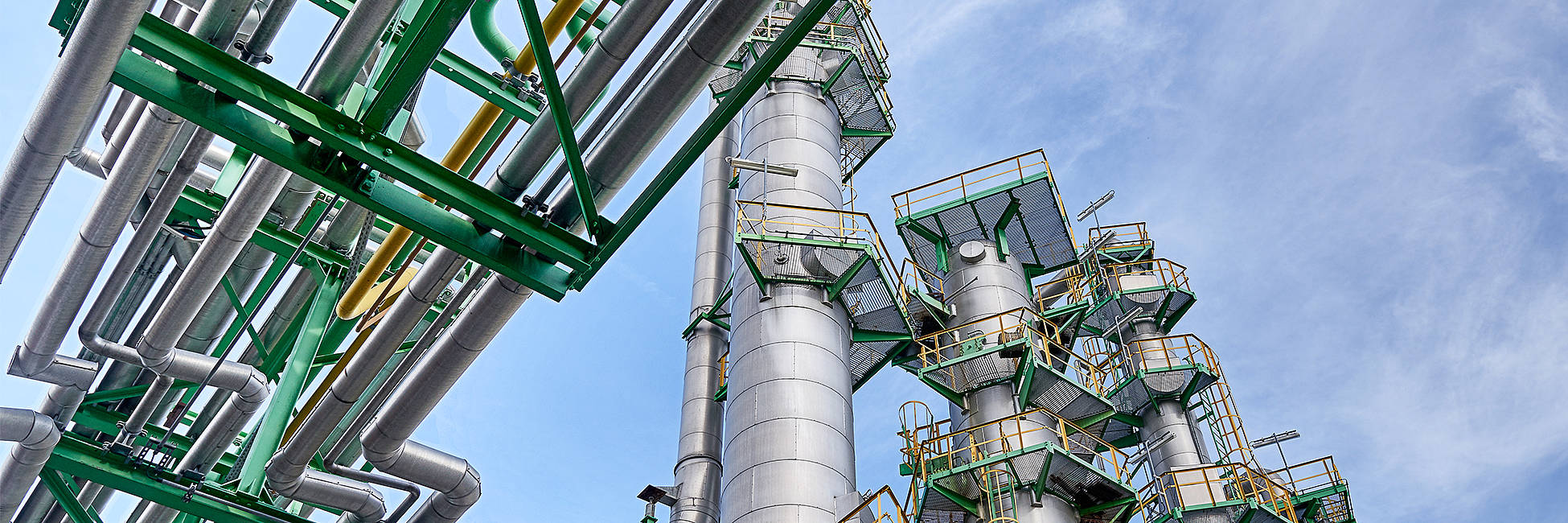
Today's methanol plants have to comply with very detailed ecological requirements regarding the use of synthesis gas. Special attention is given to the responsible use of the large quantities of residual CO2 created by the massive amount of heat generated during the synthesis of methanol.
Through its subsidiary, CRYOTEC, which has concentrated on the intelligent use of residual gases for decades, EPC can offer an exceptionally environmentally friendly CO2 recovery process. Recycling waste products advantageously creates a win-win situation. After separating the carbon dioxide from the flue gas, the plant owner decides whether to use the CO2 himself by recycling it back into the process, and thereby increase the plant's capacity by around 30 percent or, after purification, to supply the ultrapure CO2 to, for example, the food and beverage industry.
There are many different ways of producing formaldehyde and they are subject to a number of determining factors. From a range of different catalysts, the specialists at EPC select the catalysts most suitable for the given commercial conditions and the desired quality of the end products. The reaction and temperature are controlled to optimize the product qualities, such as the various viscosities required.
EPC can construct complete plants that use an automated process and reaction control system to manufacture the desired end product. It goes without saying that we offer not only a turnkey realization but also a viability review of the plant, as well as a wide selection of modern technologies.