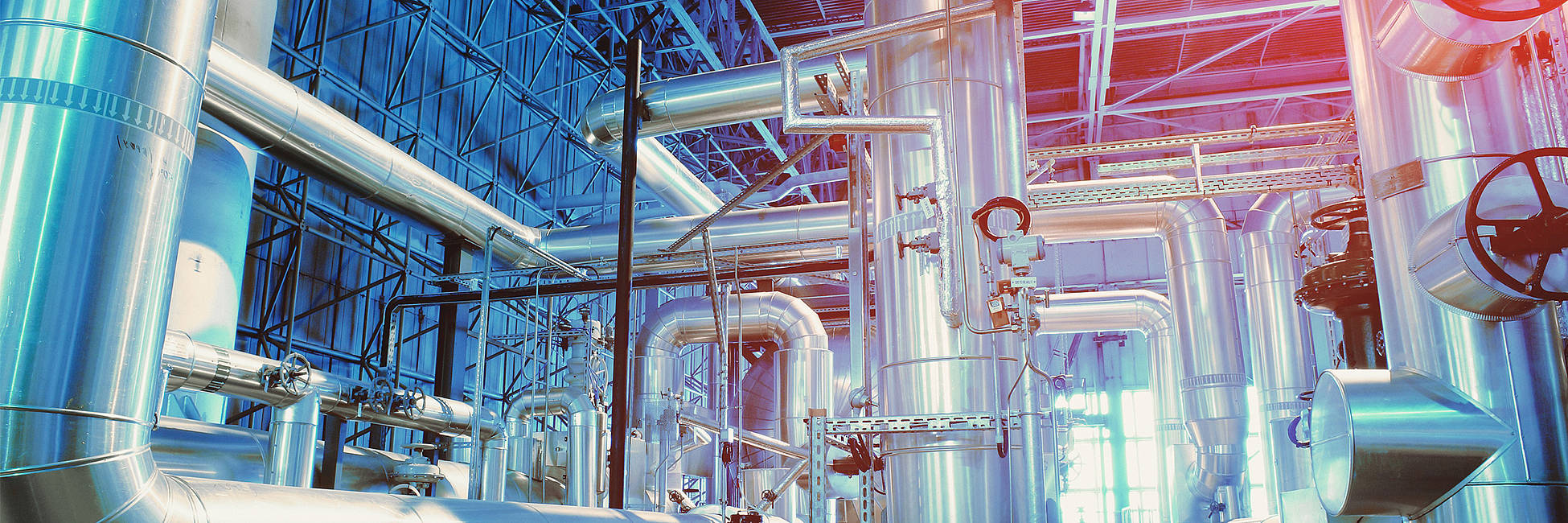
In the course of the customary life cycle of an industrial system, 40 to 50 years, it is repeatedly rebuilt, modernized and optimized: in many cases, revamping (=modernization) or de-bottlenecking (=increasing capacity) is the right answer in order to restore competitiveness and to be able to fulfill market requirements. The EPC Group provides tailor-made solutions for refurbishment of existing systems. Our task in this is to localize and remove existing bottlenecks by achieving the optimum between the investment costs and the plant output and thus increasing the quantity and also the quality of the products.
The system which guarantees constant product safety. To be able to react to a new market development, modernization of existing systems alone is mainly sufficient. The EPC Group is your experienced partner. In the first phase of modernization, we assess and analyze your system and thus create the foundation for the feasibility study, which identifies all the bottlenecks and potentials. Taking the local conditions and the future requirements of the market into due account, we draw up various realiable reconstruction concepts. The feasibility study also looks at the operating costs before and after refurbishment; frequently, the fixed costs can be significantly reduced. The direct comparison of the various concepts makes it possible to determine the optimum between the investment costs, the plant output and the operating costs after the reconstruction.
After the objectives of the plant refurbishment have been set, there is basic engineering followed by detail engineering, procurement and the supply of the necessary equipment, the switch-off of the system, the installation of new components and equipment and/or renewal of the existing components and, finally, restart of production without any undue delay.
The EPC Group provides customer-orientated refurbishment concepts matching requirements to maximize your system profitability with minimum refitting requirements and shortest operating standstill times. Revamping is the most cost-effective alternative compared with investing in a new system. The return on invest takes place within less than 2 years as a rule, depending on the system configuration, In most cases, the main reactors need not be replaced, as for example in our revamp concept for PET systems. Operating security, product qualities and production capacities are increased by a multiple, depending on the basic design of the system and the spatial situation on site.