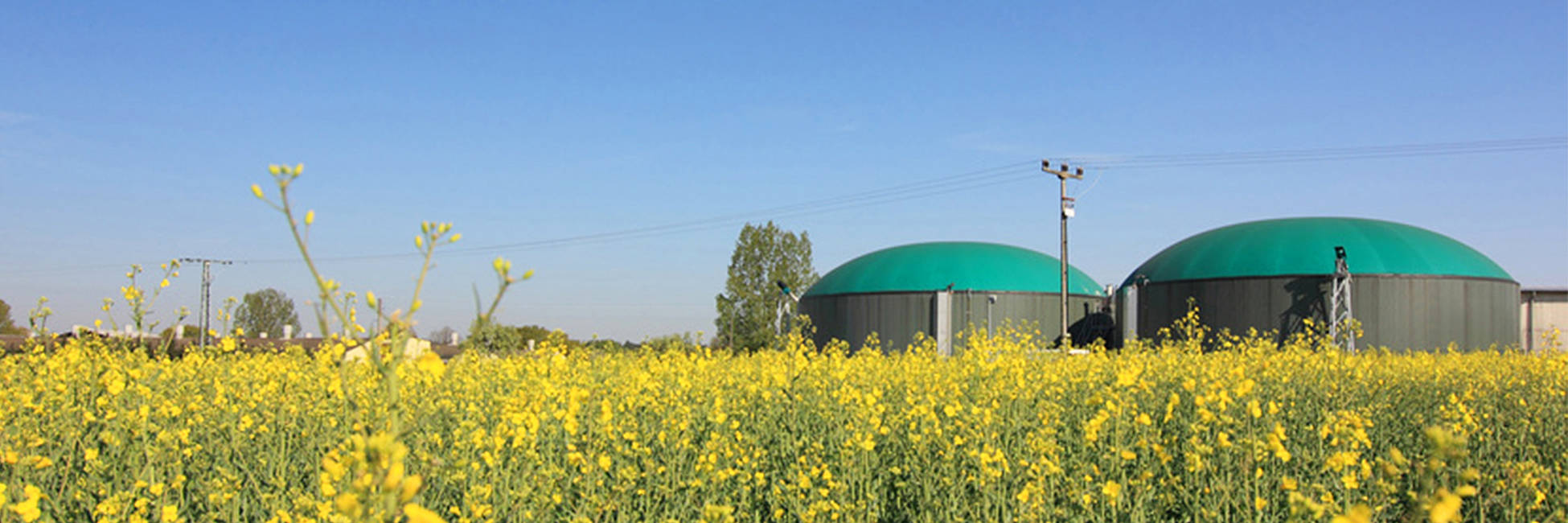
Biodiesel has established itself as a fuel in the market on account of its many advantages and positive environmental properties. Using second generation raw materials, such as jatropha and algae, specifically avoids a conflict of interests with the foodstuffs industry. Biodiesel can be mixed with conventional diesel without any problems. The quality of the biodiesel produced in plants constructed by EPC meets the fuel standard EN 14214.
Biodegradability, the positive CO2 balance in the combustion, and the potential for reducing the amount of CO2 emitted during the production of biodiesel make important contributions towards protecting the environment.
The EPC Group offers its customers complete biodiesel production plants. Their integrated business concept enables byproducts to be exploited materially or energetically. This reduces the amount of waste materials to a minimum or converts them into recyclable products. Cost-effective, efficient logistics and system structures are essential for running a plant profitably. EPC offers plants for receiving, drying and cleaning oilseeds, oil extraction plants, degumming and deacidification plants, transesterification plants, tank farms, as well as the necessarily ancillary and supply facilities. Downstream plants for converting the glycerine phase – created as a byproduct – into pharmaceutical quality glycerine can be integrated into the plant concepts. The capacities of biodiesel plants are adapted to meet the customers' requirements. The size of the raw material and final product storage are also adjusted to match the regional circumstances. A high-quality raw material is required to produce high-quality biodiesel. According to the size of the plant, we can use cold-pressing, hot-pressing or extraction systems to obtain the oil. Cold-pressing systems are suitable for smaller plants producing up to 10,000 tons of oil per year. Hot-pressing systems are used in plants with higher capacities, although they require additional infrastructure, such as a steam generator. Hexane extraction systems are used in plants with a capacity exceeding 100,000 tons of oil per annum. The extraction of the vegetable oil leaves a residue called press cake or extraction residue, the extraction meal. This residue can be marketed as valuable fodder. The glycerine phase formed during the transesterification process is also processed and concentrated to above 80% to create a saleable product.
An additional processing stage can bring the glycerine up to pharmaceutical quality. However, such complex plants are only efficient if the sections of the plant have optimal energetic integration, viable energy recovery, and make full use of the energy supplied. The efficiency of a plant can also be increased by designing the ancillary systems correctly. Our company supplies its customers with efficient, holistic solutions from one source that range up to a central, higher-level control system.