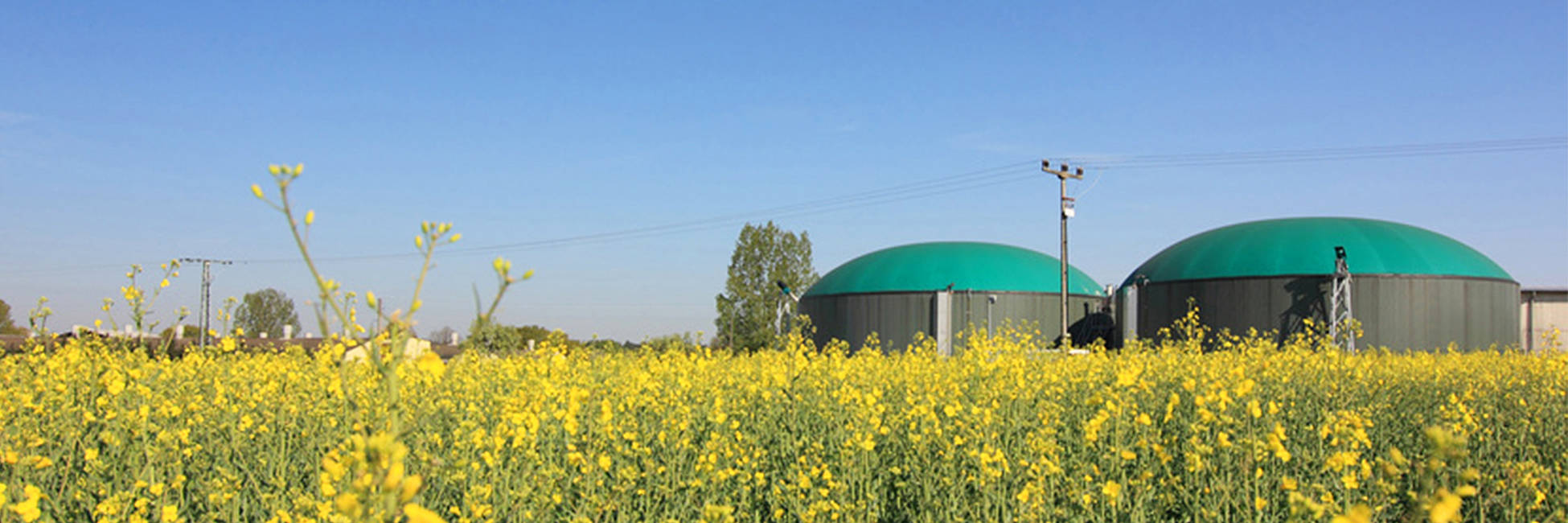
Die biologische Abbaubarkeit, die positive CO2-Bilanz bei der Verbrennung sowie das CO2-Minderungspotential bei der Produktion des Biodiesels tragen einen wichtigen Anteil zum Umweltschutz bei. Die EPC Group bietet ihren Kunden Komplettanlagen zur Biodieselherstellung an. Diese ermöglichen aufgrund ihres betriebswirtschaftlichen Gesamtkonzeptes auch eine stoffliche oder energetische Verwertung der Nebenprodukte. Somit werden Abfallstoffe auf ein Minimum reduziert oder in verwertbare Produkte überführt. Um eine Anlage wirtschaftlich betreiben zu können, sind vor allem kostengünstige und effektive Logistik- und Anlagenstrukturen notwendig. EPC bietet Anlagen, beginnend von der Annahme, Trocknung und Reinigung von Ölsaaten über Ölgewinnungsanlagen, Entschleimungs- und Entsäuerungsanlagen, Umesterungsanlagen bis hin zu Tankanlagen und den erforderlichen Neben- und Versorgungseinrichtungen.
Auch nachgeschaltete Anlagen zur Aufarbeitung der als Nebenprodukt entstehenden Glycerinphase zu Glycerin in pharmazeutischer Qualität können in die Anlagenkonzepte integriert werden. Der Aufbau der Biodieselanlagen wird entsprechend den Kundenbedürfnissen auf die gewünschte Kapazität angepasst. Die Größe der Rohstofflager und Endproduktlager wird auf die regionalen Gegebenheiten zugeschnitten. Zur Herstellung eines qualitativ hochwertigen Biodiesels ist ein hochwertiges Rohstoff notwendig. Zur Ölgewinnung können wir je nach Anlagengröße Kaltpress-, Warmpress- oder Extraktionsanlagen anbieten.
Für kleinere Anlagen bis 10.000 Jahrestonnen Öl bieten sich Kaltpressanlagen an. Für höhere Kapazitäten werden Warmpressanlagen eingesetzt, jedoch benötigt man hierzu zusätzliche Infrastruktur wie z.B. zur Dampfversorgung. Für Anlagen über 100.000 Jahrestonnen Öl werden Hexanextraktionsanlagen eingesetzt. Neben dem Pflanzenöl entsteht ein Pressrückstand, genannt Presskuchen bzw. ein Extraktionsrückstand, das Extraktionsschrot. Dieser Rückstand kann als wertvolles Futtermittel vermarktet werden. Auch die im Umesterungsprozess entstehende Glycerin-phase wird aufbereitet und auf über 80 % aufkonzentriert, so dass ein verkaufsfähiges Produkt entsteht. In einer weiteren Auf-bereitungsstufe kann das Glycerin auf eine pharmazeutische Qualität gebracht werden.
Effektiv werden jedoch solche komplexen Anlagen nur mit einer optimalen, energetisch ausgereiften Verknüpfung der Teilanlagen untereinander sowie durch sinnvolle Energierückgewinnung und volle Energieausnutzung. Auch durch die richtige Auslegung der Nebenanlagen kann die Effizienz der Anlage gesteigert werden. Durch unser Unternehmen erhalten unsere Kunden ganzheitliche, effiziente Lösungen aus einer Hand bis hin zu einem zentralen übergeordneten Leitsystem.
Das Verfahren zur Herstellung von Reinstsilicium aus metallurgischem Silicium beruht auf der thermischen Zersetzung von hochrein rektifizierten Chlorsilanen bzw. Silanen zu Silicium, unter Abspaltung und Rückführung von gasförmigen Nebenprodukten. Die kommerziell übliche Technologie verläuft über die Herstellung von Trichlorsilan im Wirbelschichtreaktor aus metallurgischem Rohsilicium und Chlorwasserstoff mit anschließender mehrstufiger Rektifikation des Trichlorsilans bis zur erforderlichen Reinheit für die gewünschte Anwendung (solar grade, electronic grade). Bei der Verwendung von Trichlorsilan für die thermische Zersetzung zu Silicium bei 900 °C im CVD-Reaktor (chemical vapor deposition) entsteht ein Gemisch aus gasförmigen Nebenprodukten, welches zur Rückführung in den Prozess aufbereitet werden muss (vent gas recovery). Der von uns optimierte Prozess der Herstellung von Reinstsilicium über Monosilan bietet eine wesentlich höhere Effektivität (Temperaturen von lediglich ca. 600 °C, Abscheidegrad von nahezu 100 % im Vergleich zu 25 %). Die Gewinnung von Monosilan erfolgt durch Disproportionierung von Trichlorsilan mit Kreislaufführung der Disproportionierungsprodukte, Trichlorsilan wird also in beiden Verfahren benötigt.
Das Produktgasgemisch aus der thermischen Zersetzung von Trichlorsilan im CVD-Reaktor (chemical vapor deposition) muß wieder in seine Bestandteile zerlegt werden, um entsprechende Produktkreisläufe installieren zu können. Das Monosilan-Verfahren bedarf dieser Kreisläufe nicht, die Vent Gas Recovery ist aber ebenfalls Bestandteil unseres Leistungsspektrums.