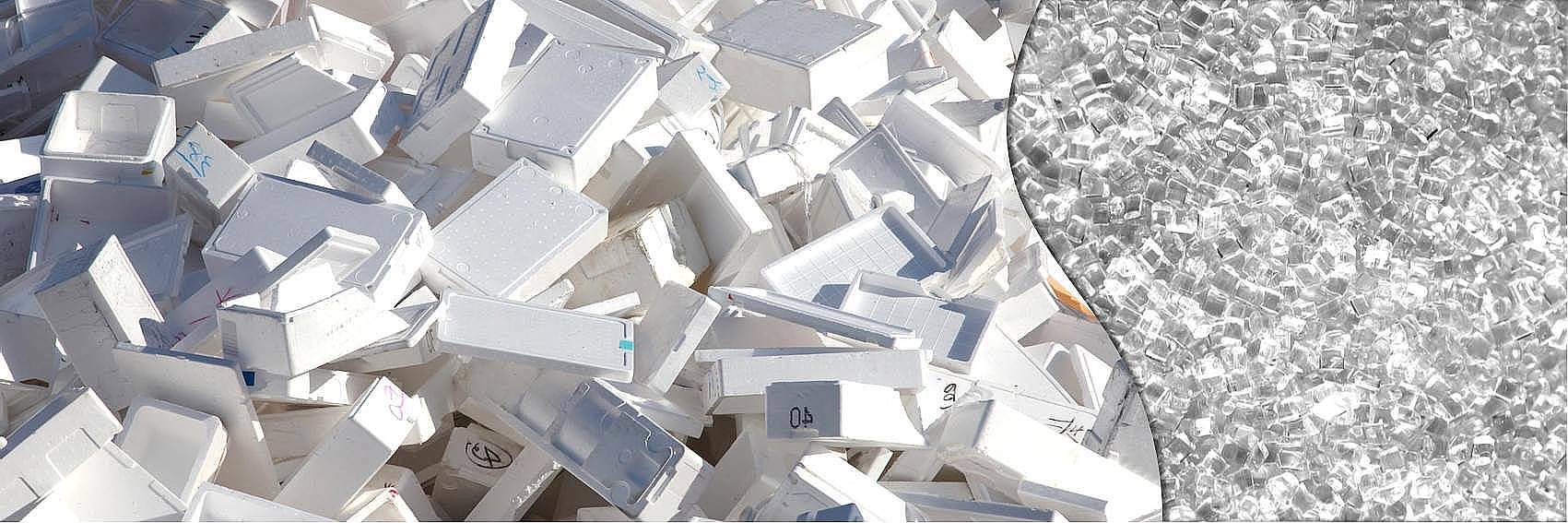
EPC’s Recyclinganlagen für expandiertes Polystyrol (EPS) arbeiten nicht nur hoch effizient, sondern bieten eine profitable und umweltfreundliche stoffliche Verwertung für unterschiedliche PS (Polystyrol) und EPS-Abfälle. Die Entwicklung des Verfahrens erfolgte in Zusammenarbeit mit dem renommierten Fraunhofer-Institut (IVV Freising) und der CreaCycle GmbH. Das resultierende CreaSolv® Verfahren erzeugt aus PS und EPS Abfällen ein hochreines PS Recyclat als Endprodukt.
Verschiedene, aufeinander abgestimmte Reinigungsschritte, der Einsatz ausgewählter CreaSolv® Formulierungen und speziell zugeschnittene Trenn- und Filtrationsschritte, entfernen dabei effizient verschiedenste Verunreinigungen. Dazu zählen auch EPS Additive wie HBCD (Hexabromcyclododecan), das bis unter die zulässigen Grenzwerte abgereichert werden kann. Das Endprodukt ist ein hoch reines und geruchsneutrales PS-Granulat. Im Vergleich zu herkömmlichen mechanischen Recyclingverfahren, die im Polystyrol enthaltene Schad- und Gefahrstoffe nicht ausschleusen können, erzeugen EPS-Recyclinganlagen von EPC nach dem CreaSolv® Verfahren Polystyrol mit hoher Reinheit. Dieses Verfahren bietet darüber hinaus große ökologische Vorteile gegenüber den bisher angewandten Entsorgungsmethoden für EPS/ PS haltige Abfälle.
EPS ist nicht nur ein gängiges Verpackungsmaterial, sondern wird seit über 50 Jahren als Dämmstoff eingesetzt und hat sich z.B. in Deutschland an Außenwänden einen Anteil von über 80% erobert. Bis 2015 wurde diese EPS-Isolierung mit HBCD ausgerüstet, dessen Produktion und Einsatz heute weltweit verboten ist. HBCD befindet sich auf der sogenannten POP Liste (persistent organic pollutant) und Abfälle, die diesen Stoff enthalten, müssen rückstandsfrei zerstört werden, womit in Zukunft ein mechanisches Recycling nicht mehr möglich ist und nur noch die kostenpflichtige Müll-Verbrennung bleibt.
Für Müllverbrennungsanlagen ist EPS mit seinem hohen Heizwert allerdings eine Herausforderung und kann nur zusammen mit anderen Abfällen in niedriger Konzentration mit verbrannt werden. Neben der Verbrennung oder Deponierung von Gefahr- und Schadstoffhaltigen EPS/PS Abfällen steht mit der EPC Anlagentechnik zum Recycling von EPS nach dem CreaSolv® Prozess jetzt zum ersten Mal ein geschlossener ökonomischer und wirtschaftlicher Wertstoffkreislauf für PS-haltige Abfallströme zur Verfügung, der das „Circular Economy“ Konzept der der Europäischen Union erfüllt.
Im Gegensatz zu etablierten mechanischen Reinigungsverfahren kann das EPS Recycling mit der CreaSolv® Technology Stoffströme mit Verunreinigungen und Gefahrstoffen verarbeiten. Sowohl Anhaftungen, eingebettete Verunreinigungen, eingebettete Gefahrstoffe und auch Geruchsstoffe werden mit der CreaSolv® Technology zuverlässig aus dem Eingangsstrom entfernt bzw. abgereichert (z.B. Einhaltung aktuelle POP Regularien). Ausgehend von unseren Standarddesigns der EPS CreaSolv® Recycling Anlagen sind jederzeit individuelle Anpassungen an die jeweiligen Kundenbedürfnisse möglich. Auch bieten wir unseren Kunden produktionsbegleitende F&E Leistungen innerhalb unseres Aftersales Service. Diese Flexibilität bietet unseren Kunden und der Umwelt einen deutlichen Mehrwert gegenüber den bekannten und etablierten Verfahren.
EPC variPLANT® verschafft Ihnen folgende Wettbewerbsvorteile:
EPC PETvantage® ist vor allem in Hinblick auf die Qualitätssicherung und damit Wettbewerbsfähigkeit äußerst gewinnbringend:
EPC inside PET® ist eine von EPC entwickelte Betriebssoftware für einen vollautomatischen Anlagenbetrieb und die Qualitätssteuerung für Anlagen mit dem innovativen EPC-Polyesterprozess. Mit EPC inside PET® werden Qualitätsschwankungen der Rohstoffe kompensiert. Bei bestehenden Anlagen wird die Gleichmäßigkeit der Endprodukte durch die umfassende und intelligente Prozesskontrolle deutlich verbessert. Wir bieten EPC inside PET® als eigenständige Lösung oder in Kombination mit einer Prozessoptimierung und Kapazitätssteigerung, unserer bewährten EPC PETvantage®-Technologie, an.
Wirtschaftliche und qualitative Vorteile von EPC inside PET®:
Das hocheffiziente und flexible kontinuierliche Hydrierungsverfahren von EPC garantiert eine umsetzbare Produktion von hochwertigem CHDM. Eine hochmoderne CHDM-Produktionslinie ermöglicht eine kontinuierliche Versorgung mit ausgezeichnetem CHDM als Rohstoff für die Herstellung von hochwertigen Polyester Granulat für die schnell wachsenden technischen Anwendungen in der Elektronik-, Lebensmittel- und Medizinverpackung, Bauteilen und Konsumgütern.
Mit ihrer modernen CHDM-Hydrierungstechnologie sowie ihrer langjährigen Erfahrung in der Polymer- und Faserindustrie bietet die EPC Gruppe komplette Engineering-Pakete für die Bereitstellung von innovativen Polymer- und Faserherstellungsanlagen an.
Bei dem Veredlungsprozess wird der Polymerrohstoff in einem Mischer mit den gewünschten Zusatzstoffen versetzt und im Extruder eingearbeitet. Die Schmelze wird anschließend in einer Kühlwanne wieder verfestigt und nach dem Erstarren im Granulator geschnitten. Mit dem Masterbatch-Prozess bietet EPC seinen Kunden die Möglichkeit zu schnellen Produktwechseln innerhalb der Anlage bei einem geringen Reinigungsaufwand. Energieeffiziente Extrudersysteme sind wirtschaftlich und nachhaltig. Die Abwärme aus den Extrudern wird in die Gesamtanlage zurückgeführt und genutzt.
Das von EPC entwickelte Verfahren kann ohne größere Investitionskosten oder lange Modernisierungszeiten auch in bestehenden Anlagen durchgeführt werden. Mittels einer speziellen Vorrichtung wird Stickstoff in bis zu 16 Extraktionszonen der Kolonne verteilt. In der Vorrichtung strömt Granulat in einer Schüttschicht von oben nach unten. Der Stickstoff und das Extraktwasser werden im Gegenstrom nach oben geführt. Die Vorrichtung besteht aus übereinander angeordneten Böden. Stickstoff wird beim Passieren der Böden in den Querschnitt der Kolonne verteilt. Diese Böden sind ausgeführt mit Verengungen und einem vereinten Gasraum, gebildet aus Verteilerrippen und einem peripheren Ringraum. Die Möglichkeit zum Druckausgleich des Stickstoffes im Boden ergibt sich durch die definierten Spalten in den Verteilerrippen zum Eintritt und gleichmäßigen Wieder-Austrag des Gases in den Kolonnenquerschnitt für den Fall von Druckunterschieden zwischen den Verengungen und dem Bodenraum infolge unterschiedlicher Gasmengen.
Vorteile der durch EPC patentierten Lösung:
Das von EPC entwickelte Reaktormaterial, welche auf einer speziellen Aluminium-Legierung basiert, ist inert gegenüber den Reaktionsbedingungen (kein Materialabtrag) und hat im Gegenzug keinen Einfluss auf das Reaktionsmedium (kein unkontrolliertes Reaktionsverhalten). Das Material wird für den Reaktor sowie für vor- und nachgelagerte Prozessstufen im Zusammenhang mit der Polymerisationsreaktion verwendet. Anlagenteile aus diesem Material müssen über die gesamte projektierte Anlagenlaufzeit nicht ausgetauscht werden.
Durch die Vermeidung von Ablagerungen verlängern sich die Produktionszyklen. Die Notwendigkeit, seltener reinigen zu müssen, erhöht die Produktionskapazität und verringert den Einsatz von Reinigungsmitteln. Das Material weist Festigkeitseigenschaften ähnlich wie Stahl auf und lässt sich mit den gängigen Bearbeitungs- und Umformverfahren (Walzen, Biegen, Schleifen, Polieren, Schweißen) bearbeiten.
Die Technologie
Mit EPC variPILOT sind Sie gut beraten: Bevor wir Ihre Pilotanlage konfigurieren, machen wir eine Bestandsaufnahme vor Ort und legen den zukünftigen Standort fest. Entsprechend den Gegebenheiten, den Produktparametern sowie Ihren Anforderungen planen und konstruieren wir Ihre spezielle Versuchsanlage. Für eine schnelle und unkomplizierte Installation und Inbetriebnahme wird Ihre variPILOT – Anlage von uns vormontiert geliefert.