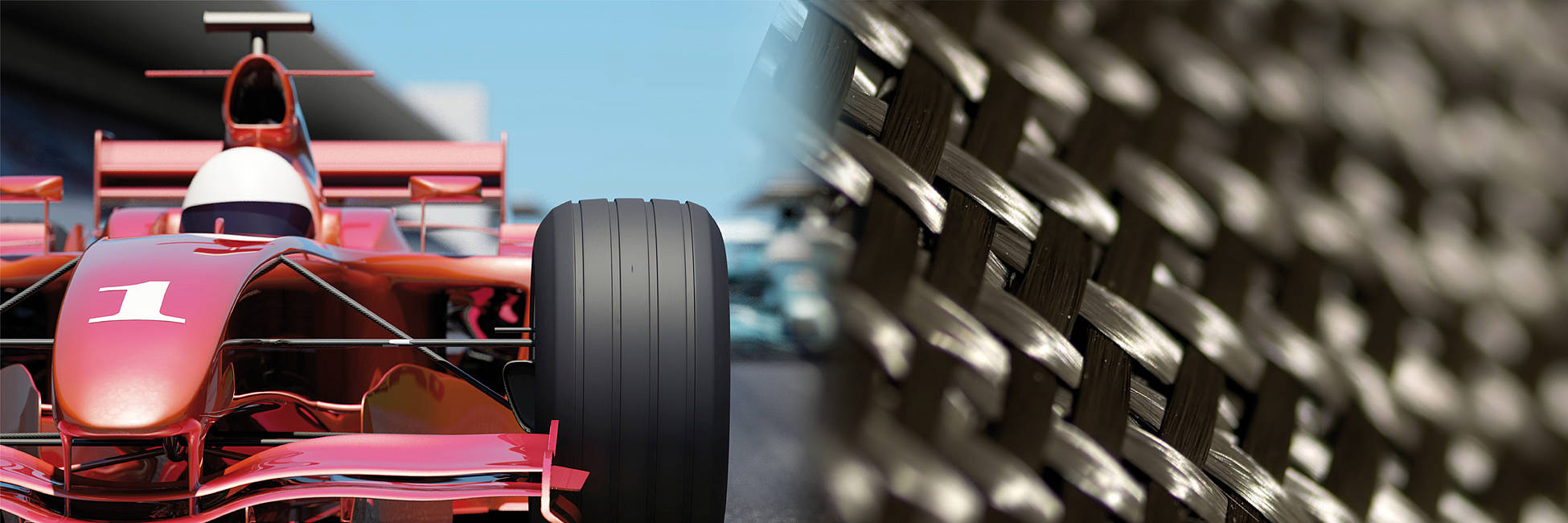
Die etablierten Kohlefaserhersteller sowie Newcomer, die sich ausschließlich auf die Herstellung des letzten Schrittes, der Kohlefaserherstellung beschränken, haben mit den am Markt verfügbaren unterschiedlichen PAN-Precursorqualitäten zu kämpfen. Dabei ist einerseits die Knappheit qualitativ hochwertiger Precursor ein Problem, andererseits ist die ungleiche Qualität der verschiedenen marktgängigen Precursor für die Kohlefaserproduzenten ein Problem.
Speziell bei dem Einsatz von Kohlefasern in Hochleistungsverbundwerkstoffen für die Luftfahrt- oder Raumfahrtindustrie, der Formel 1 oder im Hochleistungsmaschinenbau sind qualitativ hochwertige und konstante PAN-Precursorqualitäten als Rohmaterial für die Kohlefaserherstellung unerlässlich, um eine Anlage wirtschaftlich betreiben zu können.
Wie allgemein bekannt, ist jede Faseranlage ein Unikat, das spezifische, exakt zu ermittelnde Einstellparameter für qualitativ hochwertige Produkte benötigt. Aus diesem Grund kann es erforderlich werden, die Precursorqualität exakt auf die Bedürfnisse der nachgeschalteten Kohlefaseranlage anzupassen. Bei nicht integrierten Produktionsanlagen d.h. dem Zukauf von Precursor ist dies praktisch kaum realisierbar. Diesem Thema hat sich die EPC Group mit weitreichenden F&E Tätigkeiten und einen in sich geschlossenen Anlagensystem angenommen.
Die Fachleute der EPC Group haben maßgeschneiderte Gesamtkonzepte entwickelt, welche auf eine integrierte Produktion beginnend mit der PAN-Polymerisation, der Herstellung der Spinnlösung, dem Verspinnen zu PAN-Precursor bis hin zur Kohlefaser bauen. Dabei integrieren wir qualitätsrelevante Nebenanlagen wie Lösemittelrückgewinnung, Aufbereitungsanlagen für Betriebsmittel sowie das sach- und qualitätsgerechte Handling der Zwischen- und Endprodukte in unser Gesamtkonzept. Durch diese gesamtheitliche Betrachtung können zum einen Synergien und Verschaltungen zur effizienten Energienutzung umgesetzt werden. Zum anderen werden damit unsere Kunden in die Lage versetzt, den Gesamtprozess zu optimieren und kontinuierlich eine hohe Ausbeute an qualitativ hochwertigen Fasern zu produzieren. Ebenfalls ist eine durchgängige Qualitätssicherung vom Rohstoff Acrylnitril bis zur einzelnen Kohlefaserspule sichergestellt. Dies ist für High-End-Anwendungen ein wichtiges Auswahlkriterium und kann zum Alleinstellungsmerkmal unserer Kunde führen.
Da uns bewusst ist, dass ein solch komplexe Produktionsanlage nicht ohne fachliche Begleitung in Betrieb genommen werden und betrieben werden kann, begleiten wir unsere Kunden bis zum Erreichen der geplanten Produktqualität Hand in Hand.
EPC variPLANT® verschafft Ihnen folgende Wettbewerbsvorteile:
EPC PETvantage® ist vor allem in Hinblick auf die Qualitätssicherung und damit Wettbewerbsfähigkeit äußerst gewinnbringend:
EPC inside PET® ist eine von EPC entwickelte Betriebssoftware für einen vollautomatischen Anlagenbetrieb und die Qualitätssteuerung für Anlagen mit dem innovativen EPC-Polyesterprozess. Mit EPC inside PET® werden Qualitätsschwankungen der Rohstoffe kompensiert. Bei bestehenden Anlagen wird die Gleichmäßigkeit der Endprodukte durch die umfassende und intelligente Prozesskontrolle deutlich verbessert. Wir bieten EPC inside PET® als eigenständige Lösung oder in Kombination mit einer Prozessoptimierung und Kapazitätssteigerung, unserer bewährten EPC PETvantage®-Technologie, an.
Wirtschaftliche und qualitative Vorteile von EPC inside PET®:
Das hocheffiziente und flexible kontinuierliche Hydrierungsverfahren von EPC garantiert eine umsetzbare Produktion von hochwertigem CHDM. Eine hochmoderne CHDM-Produktionslinie ermöglicht eine kontinuierliche Versorgung mit ausgezeichnetem CHDM als Rohstoff für die Herstellung von hochwertigen Polyester Granulat für die schnell wachsenden technischen Anwendungen in der Elektronik-, Lebensmittel- und Medizinverpackung, Bauteilen und Konsumgütern.
Mit ihrer modernen CHDM-Hydrierungstechnologie sowie ihrer langjährigen Erfahrung in der Polymer- und Faserindustrie bietet die EPC Gruppe komplette Engineering-Pakete für die Bereitstellung von innovativen Polymer- und Faserherstellungsanlagen an.
Bei dem Veredlungsprozess wird der Polymerrohstoff in einem Mischer mit den gewünschten Zusatzstoffen versetzt und im Extruder eingearbeitet. Die Schmelze wird anschließend in einer Kühlwanne wieder verfestigt und nach dem Erstarren im Granulator geschnitten. Mit dem Masterbatch-Prozess bietet EPC seinen Kunden die Möglichkeit zu schnellen Produktwechseln innerhalb der Anlage bei einem geringen Reinigungsaufwand. Energieeffiziente Extrudersysteme sind wirtschaftlich und nachhaltig. Die Abwärme aus den Extrudern wird in die Gesamtanlage zurückgeführt und genutzt.
Das von EPC entwickelte Verfahren kann ohne größere Investitionskosten oder lange Modernisierungszeiten auch in bestehenden Anlagen durchgeführt werden. Mittels einer speziellen Vorrichtung wird Stickstoff in bis zu 16 Extraktionszonen der Kolonne verteilt. In der Vorrichtung strömt Granulat in einer Schüttschicht von oben nach unten. Der Stickstoff und das Extraktwasser werden im Gegenstrom nach oben geführt. Die Vorrichtung besteht aus übereinander angeordneten Böden. Stickstoff wird beim Passieren der Böden in den Querschnitt der Kolonne verteilt. Diese Böden sind ausgeführt mit Verengungen und einem vereinten Gasraum, gebildet aus Verteilerrippen und einem peripheren Ringraum. Die Möglichkeit zum Druckausgleich des Stickstoffes im Boden ergibt sich durch die definierten Spalten in den Verteilerrippen zum Eintritt und gleichmäßigen Wieder-Austrag des Gases in den Kolonnenquerschnitt für den Fall von Druckunterschieden zwischen den Verengungen und dem Bodenraum infolge unterschiedlicher Gasmengen.
Vorteile der durch EPC patentierten Lösung:
Das von EPC entwickelte Reaktormaterial, welche auf einer speziellen Aluminium-Legierung basiert, ist inert gegenüber den Reaktionsbedingungen (kein Materialabtrag) und hat im Gegenzug keinen Einfluss auf das Reaktionsmedium (kein unkontrolliertes Reaktionsverhalten). Das Material wird für den Reaktor sowie für vor- und nachgelagerte Prozessstufen im Zusammenhang mit der Polymerisationsreaktion verwendet. Anlagenteile aus diesem Material müssen über die gesamte projektierte Anlagenlaufzeit nicht ausgetauscht werden.
Durch die Vermeidung von Ablagerungen verlängern sich die Produktionszyklen. Die Notwendigkeit, seltener reinigen zu müssen, erhöht die Produktionskapazität und verringert den Einsatz von Reinigungsmitteln. Das Material weist Festigkeitseigenschaften ähnlich wie Stahl auf und lässt sich mit den gängigen Bearbeitungs- und Umformverfahren (Walzen, Biegen, Schleifen, Polieren, Schweißen) bearbeiten.
Die Technologie
Mit EPC variPILOT sind Sie gut beraten: Bevor wir Ihre Pilotanlage konfigurieren, machen wir eine Bestandsaufnahme vor Ort und legen den zukünftigen Standort fest. Entsprechend den Gegebenheiten, den Produktparametern sowie Ihren Anforderungen planen und konstruieren wir Ihre spezielle Versuchsanlage. Für eine schnelle und unkomplizierte Installation und Inbetriebnahme wird Ihre variPILOT – Anlage von uns vormontiert geliefert.