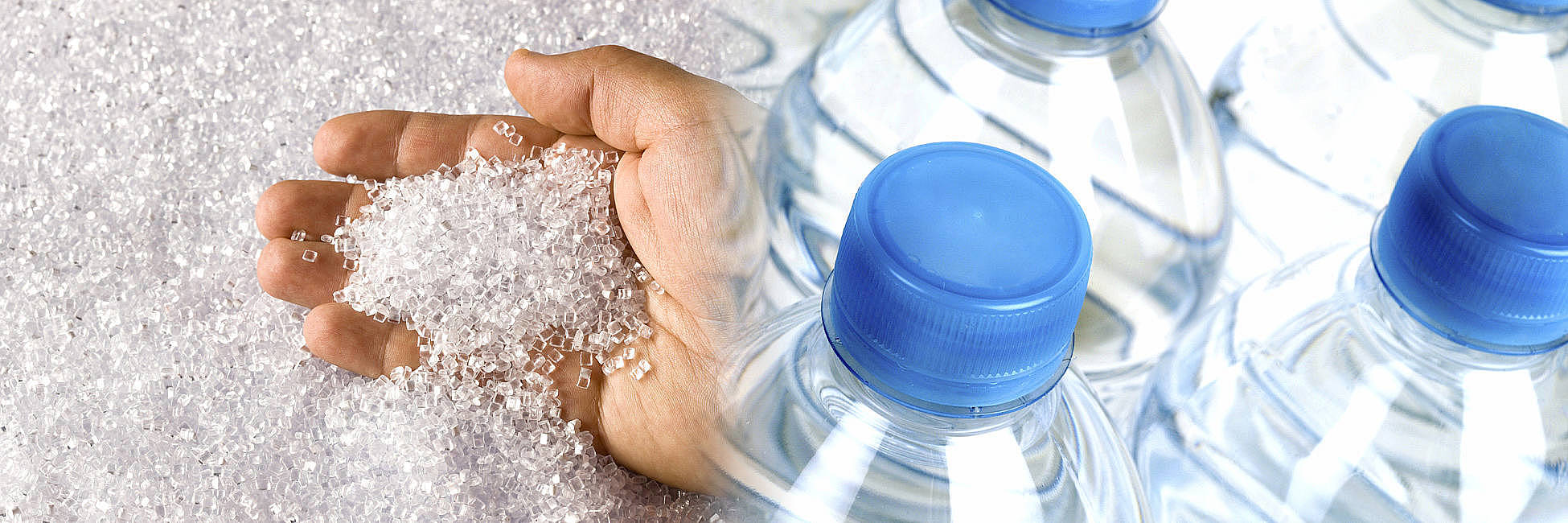
Die Überführung (Polymerisation) von niedermolekularen Verbindungen (Monomeren) zu hochmolekularen Verbindungen (Polymeren) wird dabei je nach chemischer Eigenart in den von EPC angewendeten Verfahren in Form von Polymerisation (PE, PP, PS, PVC, PAN), Polykondensation (PET, PBT, PC, PA) und Polyaddition durchgeführt.
Dabei kommen je nach Anwendungsfalls und Modifikation der gewünschten Polymere in der Regel die die Lösungspolymerisation, die Fällungspolymerisation, die Emulsionspolymerisation, die Suspensions- oder Perlpolymerisation oder die Schmelzepolymerisation zum Einsatz.
Neben der Entwicklung und dem Bau von PET-Anlagen bietet EPC eine Reihe hauseigener erprobter Technologien an, die PET-Anlagen wieder wirtschaftlich werden lassen. EPC PETvantage® ist ein patentiertes, kundenorientiertes und bedarfsgerechtes Revamping und Debottlenecking zur Maximierung Ihrer Anlagenwirtschaftlichkeit bei minimalem Umrüstungsaufwand und kürzesten Betriebsstillstandzeiten. So ist es den Ingenieuren von EPC gelungen, eine Textilfaseranlage auf PET-bottle grade Chips in Lebensmittelqualität umzustellen. Das alles bei gleichzeitiger Erhöhung der Kapazität von 440 auf mehr als 1.000 Tonnen pro Tag. Es war und ist bis heute der weltweit größte durchgeführte PET-Anlagen-Revamp - Made by EPC.
EPC bietet seinen Kunden eine breite Palette von industriellen Lösungen für die Herstellung von hochwertigen PET-G-Polymeren an:
Durch EPC insidePBT®, eine Software-Eigenentwicklung, ergeben sich für den Anlagenbetreiber erhebliche Vorteile bei der Herstellung von PBT.
Das patentierte Reaktordesign mit hydraulisch angetriebenen Wellen lässt im Vakuumbereich keine Undichtigkeiten zu und gewährt eine hohe Betriebssicherheit, da die hydraulischen Aggregate, die nicht direkt an der Welle angebracht sein müssen, in Stand-By ausgeführt werden und somit ein Ausfall ausgeschlossen werden kann. Außerdem erlaubt die Ausführung des Umesterungsystems eine einfachere und stabile Steuerung des Prozesses. Das Resultat ist eine hohe Wirtschaftlichkeit, da die Anlage durch die reduzierten Stillstandszeiten höher verfügbar ist sowie hohe und gleichmäßige Produktqualitäten liefert.
Als Nebenprodukt fällt im PTA basierten Prozess eine beträchtliche Menge an THF an, die nach der Aufbereitung in der integrierten Rückgewinnungsanlage zu hoher Qualität und Reinheit zu einem attraktiven Preis verkauft werden kann, wodurch sich die Amortisationszeit und die Wirtschaftlichkeit der Gesamtanlage noch verbessert werden.
Aus wirtschaftlichen Gründen kommt der DMT-basierte Prozess, bei dem zudem eine rentable Aufbereitung der Nebenprodukte nicht realisierbar ist, kaum zum Einsatz.
Durch eine ausgeklügelte Prozessführung kann der BDO Verbrauch minimiert werden, wodurch sowohl die Rohstoff- und die Energiekosten als auch die Belastung durch ausgeschleuste Stoffe drastisch gesenkt werden können.
Die EPC Group bietet für den Bau von PEN-Anlagen die Prozess-Technologie, die Engineering-Leistungen sowie die Ausrüstungen aber auch modulare Konzepte für kleinere Kapazitäten an, um allen Anforderungen unserer Kunden gerecht zu werden.
Das hocheffiziente und flexible kontinuierliche Hydrierungsverfahren von EPC garantiert eine umsetzbare Produktion von hochwertigem CHDM. Eine hochmoderne CHDM-Produktionslinie ermöglicht eine kontinuierliche Versorgung mit ausgezeichnetem CHDM als Rohstoff für die Herstellung von hochwertigen Polyester Granulat für die schnell wachsenden technischen Anwendungen in der Elektronik-, Lebensmittel- und Medizinverpackung, Bauteilen und Konsumgütern.
Mit ihrer modernen CHDM-Hydrierungstechnologie sowie ihrer langjährigen Erfahrung in der Polymer- und Faserindustrie bietet die EPC Gruppe komplette Engineering-Pakete für die Bereitstellung von innovativen Polymer- und Faserherstellungsanlagen an.
EPC insidePET® ist eine von EPC entwickelte Betriebssoftware für einen vollautomatischen Anlagenbetrieb und die Qualitätssteuerung für Anlagen mit dem innovativen EPC-Polyesterprozess. Mit EPC insidePET® werden Qualitätsschwankungen der Rohstoffe kompensiert. Bei bestehenden Anlagen wird die Gleichmäßigkeit der Endprodukte durch die umfassende und intelligente Prozesskontrolle deutlich verbessert. Wir bieten EPC insidePET® als eigenständige Lösung oder in Kombination mit einer Prozessoptimierung und Kapazitätssteigerung, unserer bewährten EPC PETvantage®-Technologie, an.
Wirtschaftliche und qualitative Vorteile von EPC insidePET®:
EPC PETvantage® ist vor allem in Hinblick auf die Qualitätssicherung und damit Wettbewerbsfähigkeit äußerst gewinnbringend:
EPC VARIPLANT® verschafft Ihnen folgende Wettbewerbsvorteile:
Bei dem Veredlungsprozess wird der Polymerrohstoff in einem Mischer mit den gewünschten Zusatzstoffen versetzt und im Extruder eingearbeitet. Die Schmelze wird anschließend in einer Kühlwanne wieder verfestigt und nach dem Erstarren im Granulator geschnitten. Mit dem Masterbatch-Prozess bietet EPC seinen Kunden die Möglichkeit zu schnellen Produktwechseln innerhalb der Anlage bei einem geringen Reinigungsaufwand. Energieeffiziente Extrudersysteme sind wirtschaftlich und nachhaltig. Die Abwärme aus den Extrudern wird in die Gesamtanlage zurückgeführt und genutzt.
Das von EPC entwickelte Verfahren kann ohne größere Investitionskosten oder lange Modernisierungszeiten auch in bestehenden Anlagen durchgeführt werden. Mittels einer speziellen Vorrichtung wird Stickstoff in bis zu 16 Extraktionszonen der Kolonne verteilt. In der Vorrichtung strömt Granulat in einer Schüttschicht von oben nach unten. Der Stickstoff und das Extraktwasser werden im Gegenstrom nach oben geführt. Die Vorrichtung besteht aus übereinander angeordneten Böden. Stickstoff wird beim Passieren der Böden in den Querschnitt der Kolonne verteilt. Diese Böden sind ausgeführt mit Verengungen und einem vereinten Gasraum, gebildet aus Verteilerrippen und einem peripheren Ringraum. Die Möglichkeit zum Druckausgleich des Stickstoffes im Boden ergibt sich durch die definierten Spalten in den Verteilerrippen zum Eintritt und gleichmäßigen Wieder-Austrag des Gases in den Kolonnenquerschnitt für den Fall von Druckunterschieden zwischen den Verengungen und dem Bodenraum infolge unterschiedlicher Gasmengen.
Vorteile der durch EPC patentierten Lösung:
Das von EPC entwickelte Reaktormaterial, welche auf einer speziellen Aluminium-Legierung basiert, ist inert gegenüber den Reaktionsbedingungen (kein Materialabtrag) und hat im Gegenzug keinen Einfluss auf das Reaktionsmedium (kein unkontrolliertes Reaktionsverhalten). Das Material wird für den Reaktor sowie für vor- und nachgelagerte Prozessstufen im Zusammenhang mit der Polymerisationsreaktion verwendet. Anlagenteile aus diesem Material müssen über die gesamte projektierte Anlagenlaufzeit nicht ausgetauscht werden.
Durch die Vermeidung von Ablagerungen verlängern sich die Produktionszyklen. Die Notwendigkeit, seltener reinigen zu müssen, erhöht die Produktionskapazität und verringert den Einsatz von Reinigungsmitteln. Das Material weist Festigkeitseigenschaften ähnlich wie Stahl auf und lässt sich mit den gängigen Bearbeitungs- und Umformverfahren (Walzen, Biegen, Schleifen, Polieren, Schweißen) bearbeiten.
Die Technologie
Mit EPC variPILOT® sind Sie gut beraten: Bevor wir Ihre Pilotanlage konfigurieren, machen wir eine Bestandsaufnahme vor Ort und legen den zukünftigen Standort fest. Entsprechend den Gegebenheiten, den Produktparametern sowie Ihren Anforderungen planen und konstruieren wir Ihre spezielle Versuchsanlage. Für eine schnelle und unkomplizierte Installation und Inbetriebnahme wird Ihre variPILOT – Anlage von uns vormontiert geliefert.