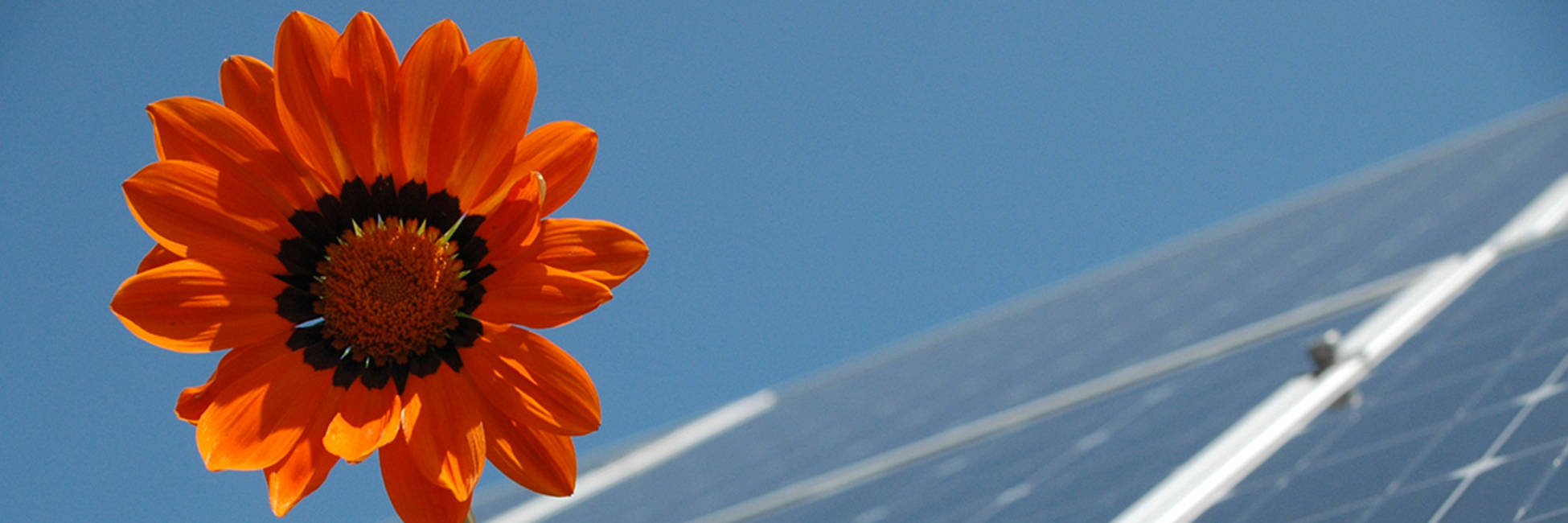
Silicon is a constituent of many minerals. Indeed it is the second most common element in the earth's crust after oxygen. Elemental silicon is used and classified in various degrees of purity. The solar industry manufactures and processes solar grade silicon (Sisg). Its impurities amount to less than 0.0001 percent. The solar industry is increasingly using even higher purities, even up to electronic grade (Sieg).
The EPC Group's portfolio of services covers not only the planning and provision of equipment for synthesizing TCS and vent gas recovery systems, but also rectification units, which require the know-how of experienced experts. We also provide you with the ancillary plants, infrastructure systems and construction planning services for complete factories. Production methods for TCS and polysilicon Elemental silicon is obtained on an industrial scale by reducing silicon dioxide with activated carbon in a melt. This produces silicon that is sufficiently pure for metallurgical purposes. However, the silicon has to be purified even further to obtain polycrystalline silicon (Sisg). This is done e.g. with the aid of a Siemens method that has been further developed by EPC.
The first step is to mix the metallurgical silicon with gaseous hydrogen chloride. This produces hydrogen, which is removed, and trichlorosilane, which is purified in further distillation stages. In the subsequent CVD process, gaseous TCS is fed into separation reactors in which ultrapure silicon is deposited on up to 54 hot silicon rods. The production cycle of each CVD reactor finishes after about 4 days, after which the polycrystalline silicon is "harvested". Silicofluidizedn tetrachloride is formed as a byproduct. This is converted back to trichlorosilane in a fluidized bed-reactor, and fed back into the production cycle. This conversion reactor can also be designed to be the sole source of TCS.
Monosilane has the simplest chemical structure of all the silanes, it is also known as silicon hydride. Silanes are part of a group of chemical compounds that consist of a silicon framework and hydrogen. Monosilane is used to separate silicon and silicon nitride layers in semi-conductor production and in the manufacture of solar cells.
EPC offers technologies for the economical and efficient manufacture and storage of monosilane. Special gases, such as monosilane, are used on account of the high requirements for purity and plant safety. We develop tailor-made and, above all, economical solutions for our customers, and also for new production technologies. Our monosilane tank, filling and distribution systems for our customers set new standards in the semi-conductor supply industry.