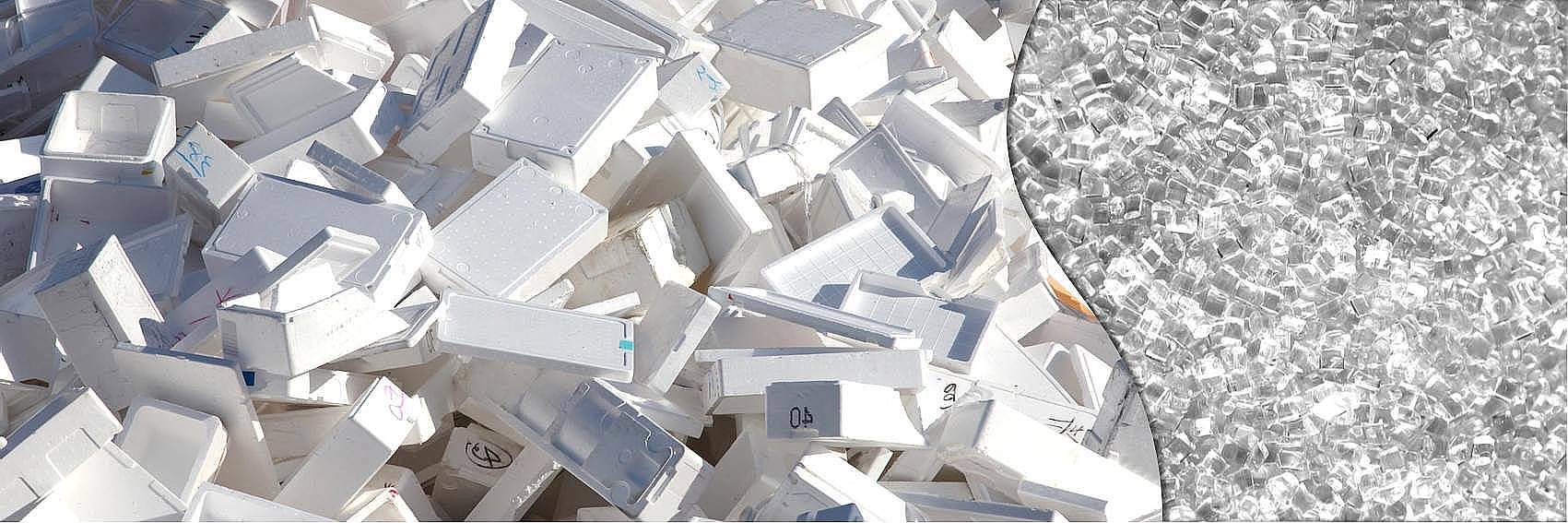
EPC's recycling plants for expanded polystyrene (EPS) are not only highly efficient, but also offer a profitable and environmentally friendly recycling for different PS (polystyrene) and EPS waste. The process was developed in collaboration with the renowned Fraunhofer Institute (IVV Freising) and CreaCycle GmbH. The resulting CreaSolv® Technology produces a high-purity PS Recyclate as a final product from PS and EPS waste.
Various precisely coordinated cleansing steps, the use of selected CreaSolv® formulations and specially tailored separation and filtration steps efficiently remove a wide range of contaminants. This also includes EPS additives such as HBCD (Hexabromocyclododecane), which can be depleted below the permissible limits. The final product is a high purity and odorless PS granulates. Compared to conventional mechanical recycling processes, which cannot extract toxic and hazardous substances contained in polystyrene, EPC’s EPS recycling plants based on the CreaSolv® Technology produce high purity polystyrene. This process also offers great ecological advantages over waste disposal methods used to date for EPS / PS waste.
EPS is not only a common packaging material, but has been used as an insulating material for more than 50 years e.g. it has been installed on over 80% of exterior walls in Germany. Till 2015 this sort of EPS insulation was equipped with HBCD, a substance of which production and use are now banned worldwide. HBCD is placed on the so-called POP list (persistent organic pollutant) and wastes that contain this substance have to be destroyed residue-free, which means that in the future, mechanical recycling is no longer possible and only the chargeable waste incineration remains. For waste incineration plants, however, EPS, with its high calorific value, is a challenge and can only be combusted together with other waste in low concentrations.
Apart from the incineration or dumping of EPS / PS wastes containing hazardous substances and pollutants, EPC’s system for recycling EPS based on the CreaSolv® process now provides an alternative close-looped economical recycling cycle for waste streams containing PS, a process that fulfills "Circular Economy" concept of the European Union. In contrast to established mechanical cleaning processes, EPS Recycling can process material streams with impurities and hazardous substances using the CreaSolv® Technology. Adhesions, embedded contaminants, embedded dangers and odors are reliably removed from the inlet stream (e.g. in compliance with current POP regulations) with the CreaSolv® Technology. Based on our standard designs of the EPS CreaSolv® recycling systems, individual adaptations according to customer requirements are possible. We also offer our customers production-accompanying R & D services within our aftersales service scope. This flexibility offers our customers and the environment a clear added value compared to the well-known and established procedures.
EPC variPLANT® gives you the following competitive advantages:
EPC PETvantage® is the most cost-effective alternative to investing in a new plant. Depending on the plant configuration, a return on the investment is usually achieved in less than 2 years. In most cases, the main reactors do not need to be replaced. Operational safety, product qualities and production capacities are increased by a multiple, depending on the basic design of the plant and the space available on site.
EPC PETvantage® generates very high profits, mainly through quality assurance and the consequent greater competitiveness:
Commercial and qualitative advantages of EPC inside PET®:
EPC Group has vast experience in the polymers and fibers industry and offers complete engineering packages in delivering world-class polymer/fiber manufacturing plants. For the production of high-quality PETG, PCT, PCTG and PCTA, EPC Group offers its modern CHDM Hydrogenation Technology for the production of top-grade CHDM.
EPC’s highly efficient and flexible continuous hydrogenation process guarantees a feasible production of top quality CHDM. Furthermore, having your own state-of-the-art CHDM production line will ensure a continuous supply of high-grade CHDM as raw material for the manufacturing of high value polyesters resin for the fast growing technical applications in electronics, food and medical packaging, construction components and consumer goods.
In the refining process, the desired additives are added to the raw polymer material in a mixer, and intermingled in the extruder. The melt is then allowed to solidify again in a cooling trough, after which it is cut up in the granulator. With the masterbatch process, EPC enables its customers to change the products their plants produce quickly and keep cleaning costs low. Energy-efficient extruder systems are long lasting, and economical because the waste heat from the extruders is fed back into the entire plant for re-use.
Theprocess patented by EPC enables the material to be optimally substituted by means of nitrogen evolution in combination with a higher pressure. This significantly reduces the extract content in the granulate, while at the same time enriching the extract water to about 18%, and achieving a considerably more consistent retention time. This minimizes fluctuations in the extraction concentration.
The extraction process developed by EPC can also be used in existing plants without requiring any large investments or lengthy modernisation times. A special device distributes nitrogen into up to 16 extraction zones in the column. Granulate flows from top to bottom through a packed bed in the device.
The nitrogen and extract water are fed upwards in a counter-flow. The extraction rate depends on the number of trays, which is determined on a case by case basis. The device consists of trays arranged one above the other. Nitrogen is distributed homogeneously through these trays.
Advantages of the solution patented by EPC:
EPC has developed a reactor material based on a special aluminium alloy that is inert under the reaction conditions (no material abrasion), and consequently has no effect on the reaction medium (no uncontrolled reaction behaviour). The material is used in the manufacture of the reactor and in the up and downstream stages involved in the polymerization reaction. Plant components made of this material do not have to be replaced during the projected lifetime of the plant.
Avoiding deposits building up lengthens production cycles. Less frequent cleaning increases the production capacity and reduces the use of cleansers. The material has strength properties similar to those of steel, and can be worked with conventional machining and forming processes (rolling, bending, grinding, polishing, welding).
The technology
Choosing EPC variPILOT® is a good decision. We examine the site, and specify the future location of your pilot plant before we configure it. We plan and construct your specific test plant in accordance with the conditions, the product parameters and your requirements. We deliver your variPILOT®plant pre-assembled, so it can be quickly and easily installed and commissioned.