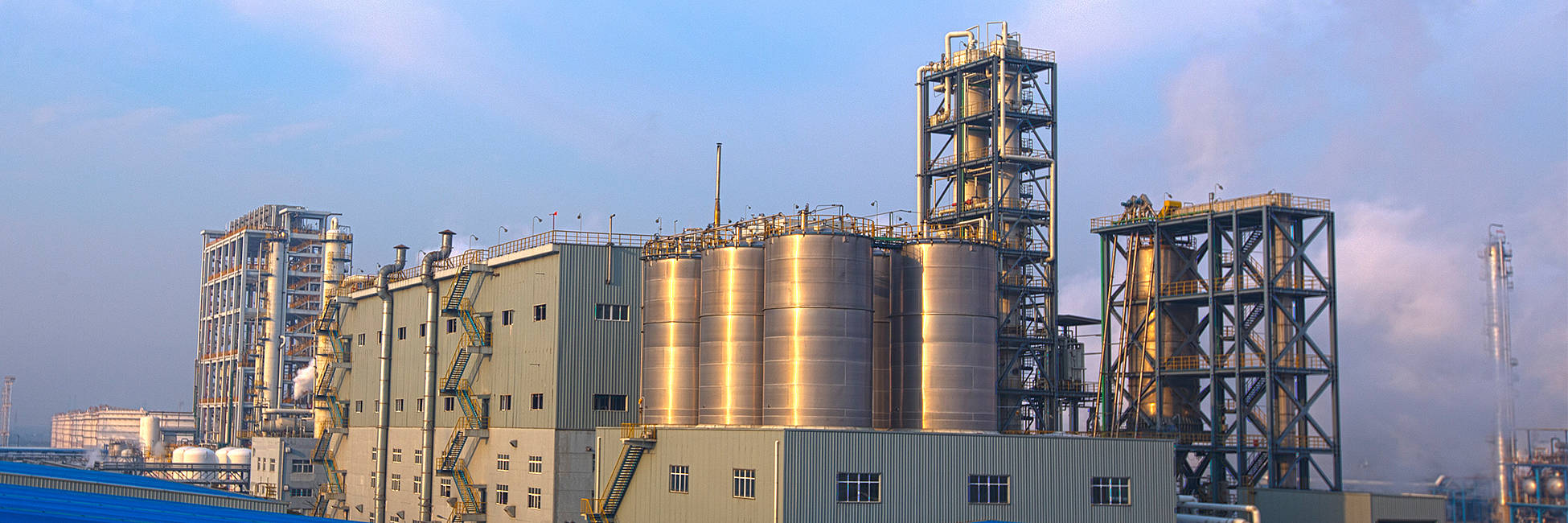
Polycarbonate (PC) has been showing its absolutely inexhaustible potential for innovations for over 50 years. New applications for this plastic come onto the market every year. Polycarbonates are often used in the production of high-tech products on account of their very good physical properties, such as low weight, temperature resistance and impact strength, as well as their brillant brightness and colorless, transparent appearance.
Of the two conventional processes, EPC has chosen the environmentally friendlier and less risky phosgene-free production path. This revolutionary patented new design ensures a top-quality polymer accompanied by a highly efficient energy balance on the foundation of comparably low investment costs. Our tailor-made plant design enables a high degree of process control to be achieved. The patented EPC reactor design facilitates variable capacities, precise setting of the MFI, and the simultaneous production of polycarbonates with different properties.
EPC Group developed the first generation of its polycarbonate production technology implementing revolutionary patented designs to ensure the production of a top-quality polymer. EPCs holistic approach to the process design resulted in an optimal energy balance and comparably low investment costs.
Now, EPC is proud to present its 2nd generation of the environmentally friendly technology that incorporates an impressive array of fine-tuning and optimization steps to ensure the continuous production of high quality polymer.
EPS Loop is a highly efficient process for removing contaminants. The process was created in cooperation with the renowned Fraunhofer Institute. It converts your EPS waste into an extremely pure PS recyclate end product – with hardly any cloudiness. A number of coordinated purification stages using, for example, solvents and special filtration, remove the contaminants efficiently. The end product is an extremely pure, odourless PS granulate, which has a great economic advantage in the market. Your PS recyclate commands a higher price in the market than other recyclates, because the EPS-Loop process achieves a higher degree of purity than conventional recycling processes.
EPC VARIPLANT gives you the following competitive advantages:
EPC PETvantage® is the most cost-effective alternative to investing in a new plant. Depending on the plant configuration, a return on the investment is usually achieved in less than 2 years. In most cases, the main reactors do not need to be replaced. Operational safety, product qualities and production capacities are increased by a multiple, depending on the basic design of the plant and the space available on site.
EPC PETvantage® generates very high profits, mainly through quality assurance and the consequent greater competitiveness:
Commercial and qualitative advantages of EPC insidePET®:
EPC Group has vast experience in the polymers and fibers industry and offers complete engineering packages in delivering world-class polymer/fiber manufacturing plants. For the production of high-quality PETG, PCT, PCTG and PCTA, EPC Group offers its modern CHDM Hydrogenation Technology for the production of top-grade CHDM.
EPC’s highly efficient and flexible continuous hydrogenation process guarantees a feasible production of top quality CHDM. Furthermore, having your own state-of-the-art CHDM production line will ensure a continuous supply of high-grade CHDM as raw material for the manufacturing of high value polyesters resin for the fast growing technical applications in electronics, food and medical packaging, construction components and consumer goods.
In the refining process, the desired additives are added to the raw polymer material in a mixer, and intermingled in the extruder. The melt is then allowed to solidify again in a cooling trough, after which it is cut up in the granulator. With the masterbatch process, EPC enables its customers to change the products their plants produce quickly and keep cleaning costs low. Energy-efficient extruder systems are long lasting, and economical because the waste heat from the extruders is fed back into the entire plant for re-use.
Theprocess patented by EPC enables the material to be optimally substituted by means of nitrogen evolution in combination with a higher pressure. This significantly reduces the extract content in the granulate, while at the same time enriching the extract water to about 18%, and achieving a considerably more consistent retention time. This minimizes fluctuations in the extraction concentration.
The extraction process developed by EPC can also be used in existing plants without requiring any large investments or lengthy modernisation times. A special device distributes nitrogen into up to 16 extraction zones in the column. Granulate flows from top to bottom through a packed bed in the device.
The nitrogen and extract water are fed upwards in a counter-flow. The extraction rate depends on the number of trays, which is determined on a case by case basis. The device consists of trays arranged one above the other. Nitrogen is distributed homogeneously through these trays.
Advantages of the solution patented by EPC:
EPC has developed a reactor material based on a special aluminium alloy that is inert under the reaction conditions (no material abrasion), and consequently has no effect on the reaction medium (no uncontrolled reaction behaviour). The material is used in the manufacture of the reactor and in the up and downstream stages involved in the polymerisation reaction. Plant components made of this material do not have to be replaced during the projected lifetime of the plant.
Avoiding deposits building up lengthens production cycles. Less frequent cleaning increases the production capacity and reduces the use of cleansers. The material has strength properties similar to those of steel, and can be worked with conventional machining and forming processes (rolling, bending, grinding, polishing, welding).
The technology
Choosing EPC variPILOT is a good decision. We examine the site, and specify the future location of your pilot plant before we configure it. We plan and construct your specific test plant in accordance with the conditions, the product parameters and your requirements. We deliver your variPILOT plant pre-assembled, so it can be quickly and easily installed and commissioned.