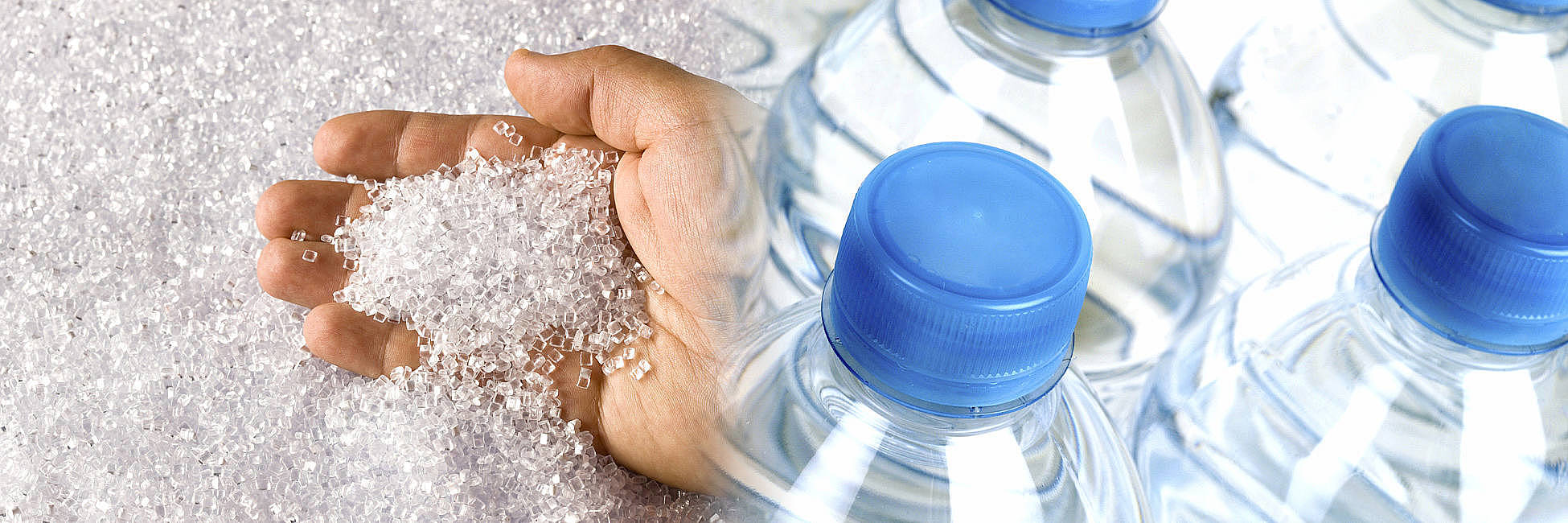
EPC uses the method appropriate to the particular chemical properties to convert (polymerise) low-molecular compounds (monomers) into high-molecular compounds (polymers) by radical, ionic or Ziegler-Natta polymerization [PE, PP, PS, PVC, PAN), polycondensation (PET, PBT, PC, PA), or polyaddition.
Solution, precipitation, emulsion, suspension or bead, or melt polymerization is used depending on which method is most suitable for the application and the modification of the desired polymers.
The PET polymer is a transparent, lightweight, strong, safe, shatterproof and recyclable material. PET in its natural state is colourless and semi-crystalline. Depending on the processing method, the PET can be semi-rigid to rigid, and it is also especially light in weight. PET makes an excellent gas and moisture barrier.
PET resin is also very sustainable as it is recyclable. It is by far the world's most recycled plastic. PET can be recycled many times – and used in food applications, personal care products, carpets, clothing and many other products.
As well as developing and constructing PET plants, EPC also offers a number of tried and tested technologies it has developed in-house, that restore PET plants to profitability. EPC PETvantage® is a patented, customer-orientated revamping and de-bottlenecking process that meets your need to maximize plant profitability with minimal retrofitting costs and the shortest plant stoppages. EPC engineers have succeeded in converting a textile fibre plant to food-quality PET bottle grade chips, and at the same time they increased the capacity from 440 to more than 1,000 tons per day. It was, and still is, the world's largest PET plant revamp – "Made by EPC".
We offer a wide range of industrial solutions for producing quality PET-G polymers:
EPC insidePBT is an in-house software development that gives plant operators substantial advantages in PBT production.
The patented reactor design has hydraulically driven shafts and prevents leaks in the vacuum range. A high level of plant safety is ensured because the hydraulic units do not have to be mounted directly on the shaft. It also has redundancy to avoid outages. The transesterification system is designed for easier and stable process control. The result is high profitability, because reduced downtimes increase availability, and the plant delivers consistently high product qualities.
A substantial quantity of THF is produced as a by-product of the PTA-based process. It can be sold at an attractive price after treatment to improve its quality and purity in the integrated recovery plant. This also shortens the amortization time and increases the profitability of the entire plant.
For commercial reasons, the DMT-based process is hardly ever used, because the by-products cannot be processed at an economic price.
Ingenious process control enables the BDO consumption to be minimized, which drastically reduces not only raw material and energy costs but also the pollution caused by emissions.
The properties of PEN place high demands on the spinning process and its pull-off forces.
The EPC Group offers not only the process technology, engineering services and the equipment for constructing PEN plants, but also modular concepts for smaller capacity plants to meet all the requirements of our customers.
EPC Group has vast experience in the polymers and fibers industry and offers complete engineering packages in delivering world-class polymer/fiber manufacturing plants. For the production of high-quality PETG, PCT, PCTG and PCTA, EPC Group offers its modern CHDM Hydrogenation Technology for the production of top-grade CHDM.
EPC’s highly efficient and flexible continuous hydrogenation process guarantees a feasible production of top quality CHDM. Furthermore, having your own state-of-the-art CHDM production line will ensure a continuous supply of high-grade CHDM as raw material for the manufacturing of high value polyesters resin for the fast growing technical applications in electronics, food and medical packaging, construction components and consumer goods.
Commercial and qualitative advantages of EPC insidePET®:
EPC PETvantage® is the most cost-effective alternative to investing in a new plant. Depending on the plant configuration, a return on the investment is usually achieved in less than 2 years. In most cases, the main reactors do not need to be replaced. Operational safety, product qualities and production capacities are increased by a multiple, depending on the basic design of the plant and the space available on site.
EPC PETvantage® generates very high profits, mainly through quality assurance and the consequent greater competitiveness:
EPC VARIPLANT® gives you the following competitive advantages:
In the refining process, the desired additives are added to the raw polymer material in a mixer, and intermingled in the extruder. The melt is then allowed to solidify again in a cooling trough, after which it is cut up in the granulator. With the masterbatch process, EPC enables its customers to change the products their plants produce quickly and keep cleaning costs low. Energy-efficient extruder systems are long lasting, and economical because the waste heat from the extruders is fed back into the entire plant for re-use.
Theprocess patented by EPC enables the material to be optimally substituted by means of nitrogen evolution in combination with a higher pressure. This significantly reduces the extract content in the granulate, while at the same time enriching the extract water to about 18%, and achieving a considerably more consistent retention time. This minimizes fluctuations in the extraction concentration.
The extraction process developed by EPC can also be used in existing plants without requiring any large investments or lengthy modernisation times. A special device distributes nitrogen into up to 16 extraction zones in the column. Granulate flows from top to bottom through a packed bed in the device.
The nitrogen and extract water are fed upwards in a counter-flow. The extraction rate depends on the number of trays, which is determined on a case by case basis. The device consists of trays arranged one above the other. Nitrogen is distributed homogeneously through these trays.
Advantages of the solution patented by EPC:
EPC has developed a reactor material based on a special aluminium alloy that is inert under the reaction conditions (no material abrasion), and consequently has no effect on the reaction medium (no uncontrolled reaction behaviour). The material is used in the manufacture of the reactor and in the up and downstream stages involved in the polymerisation reaction. Plant components made of this material do not have to be replaced during the projected lifetime of the plant.
Avoiding deposits building up lengthens production cycles. Less frequent cleaning increases the production capacity and reduces the use of cleansers. The material has strength properties similar to those of steel, and can be worked with conventional machining and forming processes (rolling, bending, grinding, polishing, welding).
The technology
Choosing EPC variPILOT® is a good decision. We examine the site, and specify the future location of your pilot plant before we configure it. We plan and construct your specific test plant in accordance with the conditions, the product parameters and your requirements. We deliver your variPILOT plant pre-assembled, so it can be quickly and easily installed and commissioned.