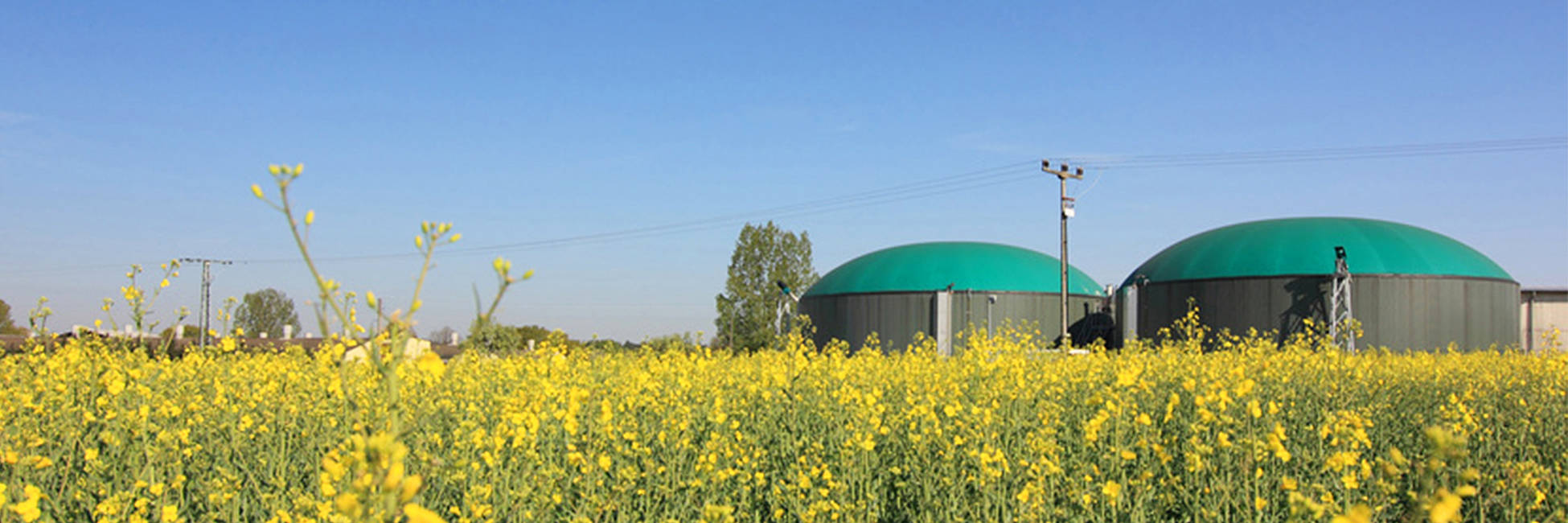
PHONE: + 49 3628 66048-2900
The use of fuels obtained from renewable raw materials and residual biological substances, and the associated utilization of the energy stored or contained in them is becoming increasingly attractive to potentially interested parties and plant owners in industrial and the recycling sector.
The main reasons for choosing biomass plants are that they give you independence from fossil sources of energy, and are an efficient and thus cost-effective way of generating energy. The EPC Group offers potential customers complete plants that can equally well use monovalent and/or bivalent fuel (a fuel mix). Wood chips (natural or waste wood) and granulated or pelleted substitute fuels made from residual material can be used as fuels. Solid residues, e.g. from the paper industry, can also be thermally utilized.
The plants offered by the EPC Group for generating energy from solid biomass comprise the following system components:
Your advantages at a glance. What you can expect from us:
Implementing system solutions all over the world is a matter of routine for us.
EPC sets up systems with which mains substitution operation is possible. Excess current can be fed into the energy supplier's network. We produce an overall, economical concept for you, attend to applications for subsidies and approvals, and construct and maintain your plants.
The method of producing ultrapure silicon from metallurgic silicon is based on the thermal decomposition of highly pure, rectified chlorosilanes or silanes to form silicon with the separation and recycling of gaseous byproducts. The conventional commercial technology passes through the stage of producing trichlorosilane in a fluidized-bed reactor from metallurgic grade silicon and hydrogen chloride. The trichlorosilane is then subjected to multi-stage rectification until the purity required for the desired application is reached (solar grade or electronic grade). The thermal decomposition of trichlorosilane in a chemical vapor deposition (CVD) reactor to form silicon at 900 °C creates a mixture of gaseous by-products, which have to be prepared for recycling (vent gas recovery) back into the process. We have optimized the process for producing ultrapure silicon from monosilane. It now offers a significantly higher efficiency as temperatures are only around 600 °C, and the collection efficiency has been increased to almost 100% in comparison to the mere 25% achieved by conventional processes. Monosilane is obtained by the disproportionation of trichlorosilane and recirculation of the disproportionation products. Trichlorosilane is thus required in both methods.
The gas mixture produced by the thermal decomposition of trichlorosilane in a chemical vapor deposition (CVD) reactor has to be separated into its constituent parts before the individual products can be recirculated. The monosilane method does not need these cycles, however Vent Gas Recovery is still part of our range or products.
The monosilane synthesis gas is stored temporarily in vacuum-insulated containers prior to further processing or filling. The containers are equipped with a pressure build-up vaporizer and an internal cooling coil to facilitate cooling. The containers are a special product of our subsidiary company, CRYOTEC, which specializes in special cryogenic applications.
Silicon tetrachloride is the main by-product of both the production of trichlorosilane from metallurgic silicon with HCl in a fluidized-bed reactor and the disproportionation of trichlorosilane. The thermal decomposition of trichlorosilane in a CVD reactor also creates large quantities of silicon tetrachloride. The silicon tetrachloride is converted with hydrogen into trichlorosilane in a conversion reactor. This process can be run homogeneously with hydrogen at approximately 1,000 °C in graphite reactors. We use the more elegant heterogeneous method of controlling the process by feeding silicon into a fluidized-bed reactor.